Level up your mass timber IQ & stay up-to-date on industry trends
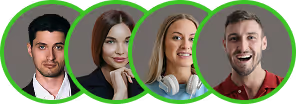
Mass timber is growing fast — but outdated beliefs are still slowing down projects, driving up costs, and creating hesitation with clients. Some AEC teams are holding onto myths that don’t match today’s reality.
Here’s the 1st of 5 myths we hear most often — and why they need to go.
At the 2025 Mass Timber Group Summit, we’re putting these myths to rest for good — backed by real project data, expert insights, and lessons learned directly from teams in the field.
This myth refuses to die — and it’s costing teams real opportunities.
On paper, direct material costs for mass timber can appear higher than steel or concrete. That’s where too many teams stop the analysis. But the smartest project teams — the ones actively delivering successful mass timber buildings — know the real math happens at the total project level, not just the materials line item.
Take 1510 Webster in Oakland, CA — a 19-storey Type IV-A building and the world’s first high-rise to use point-supported Mass Plywood Panels (MPP) from Freres Wood. After full cost comparisons with previously designed buildings in their portfolio, the developer oWOW, found that mass timber could match or beat alternative materials - to the tune of $30 Million— without compromising performance.
Where did that competitive edge come from?
✅ Lighter Structure: Mass timber’s strength-to-weight ratio reduced foundation size, excavation work, and concrete costs.
✅ Faster Assembly: The 40' x 10' MPP panels used were being installed at a rate of 1 every 15 minutes - or 6,000 sq ft every 4 hours - twice as fast as traditional steel or concrete. This minimized labor hours, field coordination, and the time the project carried construction financing.
✅ Stronger Materials = Less Materials:
"After doing independent structural testing in accordance with ASTM 119 standards that proved MPP to be more than two times stronger than CLT, we were able to make several improvements to an innovative, point-supported column connection to the floor panel; the beams were eliminated, saving 21” floor-to-floor; the floor thickness was reduced by 1” and the total number of columns were reduced by 630.” - Andrew Ball, oWOW
And that translated into direct savings on the project.
This advantage isn’t unique to Webster.
At Platte Fifteen in Denver, the project team delivered a 25% faster build compared to steel and shaved 3.5 months off a comparable concrete schedule — directly reducing financing costs and accelerating lease-up.
Mass timber’s prefabrication doesn’t just speed up structure — it reduces risk across the board:
✅ Faster dry-in = less weather exposure
✅ Prefab panels = fewer trades and faster sequencing
✅ Fewer deliveries = smoother logistics on urban sites
There’s another hidden benefit: exposed timber finishes. Mass timber’s aesthetic means less need for drop ceilings, drywall, or heavy interior finishes — all while tenants actively pay premiums for the look and feel of exposed wood.
Projects like Return to Form — a planned 12-story residential tower in Denver — are modeling this complete financial picture before ground even breaks.
Pro forma comparisons for the project show total development costs for mass timber within 0.2% of concrete once time, labor, foundation, and interior savings are factored in. That’s not a discount — it’s cost neutrality with major upside in speed, aesthetics, and carbon performance.
If your team is only comparing structural material costs in isolation, you’re not seeing the full story.
The actual cost equation for mass timber includes:
✅ Faster schedules = lower financing carry costs
✅ Lighter structure = smaller foundations and reduced excavation
✅ Fewer trades = lower coordination and labor costs
✅ Exposed finishes = reduced interior fit-out
✅ Tenant demand = faster lease-up
✅ Market differentiation = premium rental rates & easier marketability
Mass timber doesn’t need to “beat” steel or concrete on material cost alone — because that’s not how smart developers evaluate projects. When you account for total project economics — speed, risk, finishes, and tenant demand — mass timber can stand toe-to-toe with any structural system.
That’s exactly the financial reality we’ll unpack at the 2025 Mass Timber Group Summit, where the teams behind these projects just like these will share their real-world numbers and lessons learned.
👉 Secure Your Spot at the Summit