Level up your mass timber IQ & stay up-to-date on industry trends
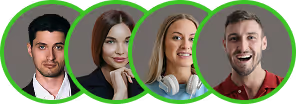
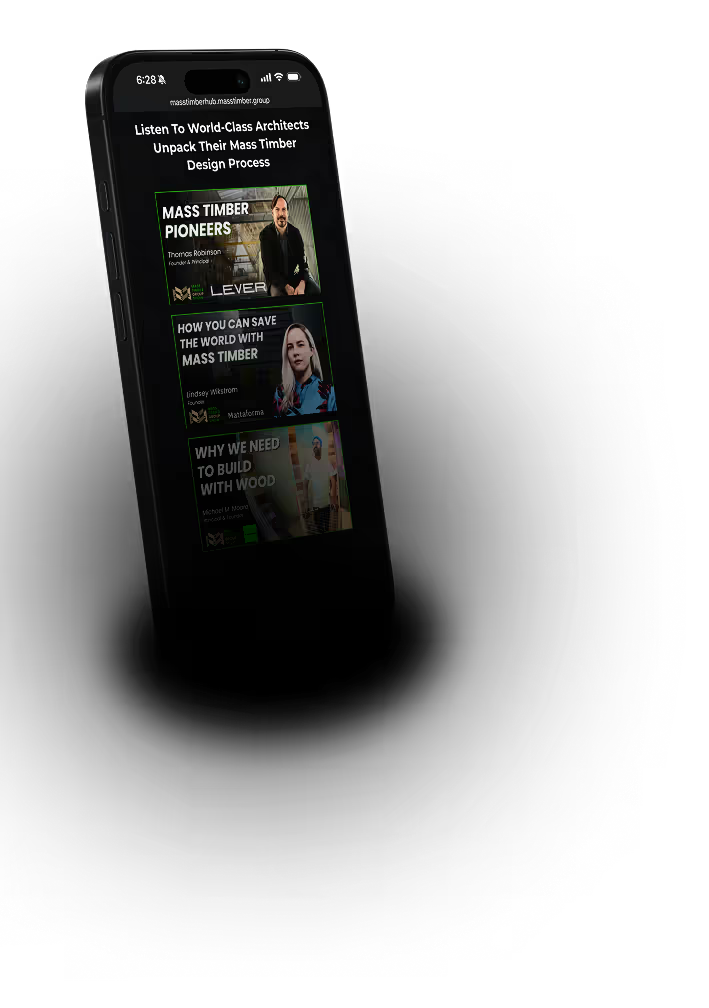
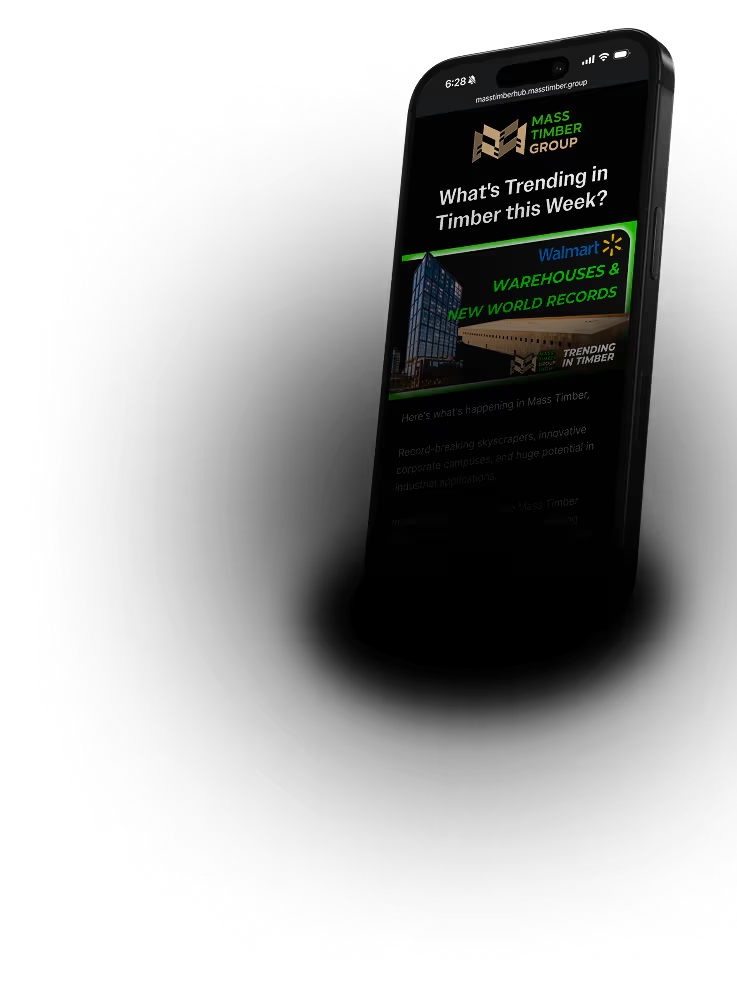
We believe that mass timber isn’t just viable. It’s the future of building
That’s what this newsletter is all about. We’re diving into the innovations, market shifts, and real-world applications proving that mass timber isn’t just possible—it’s the future. If you want to stay ahead of the curve, learn from industry leaders, and be part of the movement shaping modern construction, sign up today.
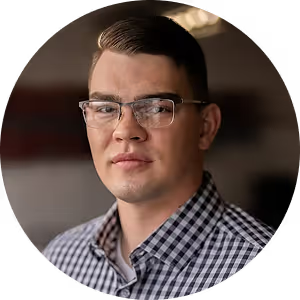
Co-founder
Mass Timber Group
$3.56B
CAP
What our community is saying
.png)
.png)
Read our recent publications
Redmond Senior Center: Pioneering Climate-Resilient Mass Timber Construction
Ever walk into a building and instantly feel a connection to nature? That's the kind of experience the design team envisioned for the new Redmond Senior & Community Center in Redmond, Washington. But this isn't just another aesthetically pleasing civic structure; it's a groundbreaking project that's pushing the boundaries of sustainable construction, particularly in its innovative use of mass timber sourced from climate-resilient forests. How did this forward-thinking project come to life, and what lessons does it hold for the future of our industry?
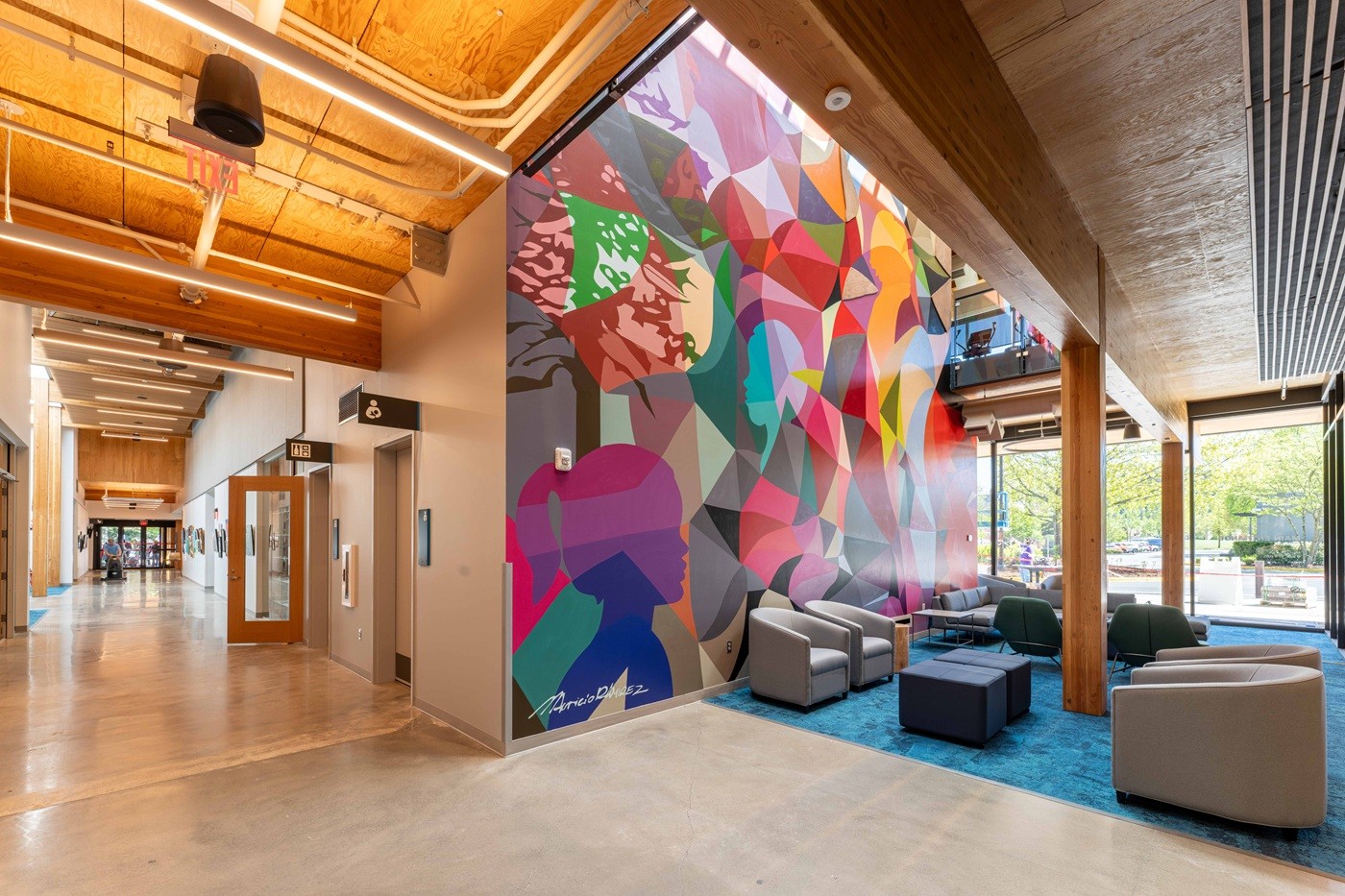
A Vision Rooted in Community and Sustainability
For five years, the City of Redmond engaged with its community, stakeholders, and seniors to define the priorities for this new center. The result is a thoughtfully designed 52,000-square-foot facility that replaces the former senior center and offers a vibrant hub for recreational events and activities for all generations, with dedicated spaces for seniors. Think of it: senior-dedicated lounges and libraries, a large multipurpose community room, active recreation areas including a flexible gym and an elevated indoor walk/jog track, and even a Kids Zone.
But the ambition didn't stop at creating a welcoming space. The City of Redmond also aimed to embody its reverence for the surrounding landscape and need to align with its Climate Emergency Declaration goals. This commitment led to a deep dive into sustainable building practices, with LEED Gold certification as a key target.
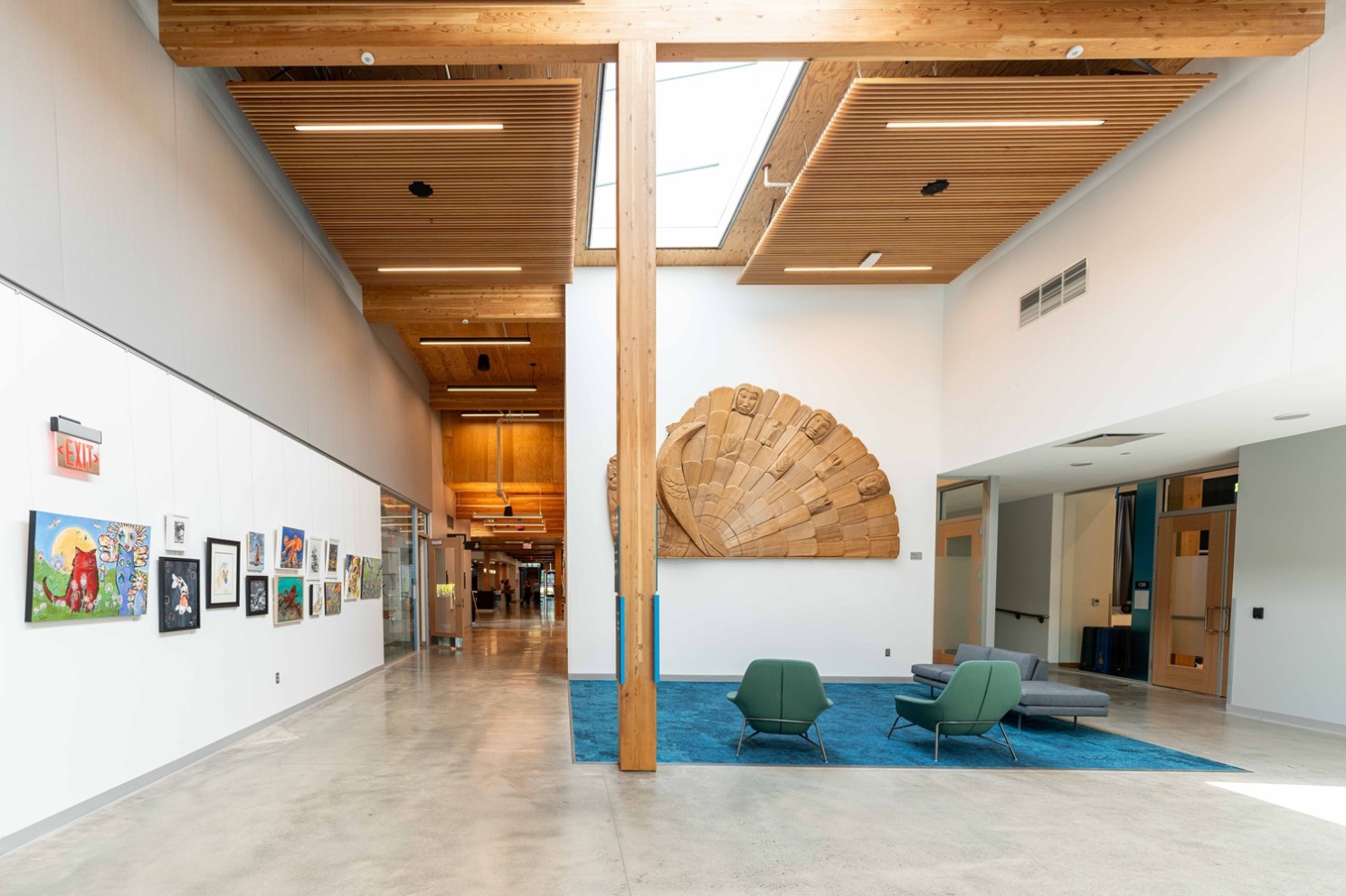
The Mass Timber Difference: More Than Just Aesthetics
The design team, led by Opsis Architecture, with Johnston Architects as the associate architect, recognized the potential of mass timber to meet both the aesthetic and sustainability goals. They opted for Mass Plywood Panels (MPP) from Freres Engineered Wood, a veneer-based engineered wood product made from Douglas-fir. Jason Fehlman, CFO and superintendent of Carpentry Plus Inc., the mass timber installer, noted, "MPP was used to create the second floor structure as well as the roof structure for the majority of the building and its versatility, with applications in an elevated track in the gymnasium, select walls, and stairs.”

Why MPP? Tyler Freres, Vice President of Sales at Freres Engineered Wood, points out a key advantage over cross-laminated timber (CLT), stating, "This double cantilever roof is a difficult thing for most wood materials to accomplish... CLT... requires more joists to support it. MPP, however, is a stronger material, allowing a single panel to cantilever in more than one direction". Fehlman of Carpentry Plus echoed this sentiment, saying, "From an unbiased perspective, MPP has a better structural performance than CLT... It’s stiffer than CLT, so it performs better when it’s cantilevering out". This structural superiority allowed for striking architectural features, like the double cantilever roof at the senior entrance with exposed MPP.
Beyond structural benefits, the exposed wood elements contribute to the building's warm and inviting atmosphere, creating a subtle nod to the outdoors. Even the gymnasium's elevated walk/jog track showcases MPP in a unique application.
A First for Climate-Resilient Wood
The Redmond Senior Center didn't just use mass timber; it pioneered the recognition of climate-resilient wood in green building. The innovation point, awarded under the innovation category, underscores the project's commitment to exceeding standard sustainable forestry certifications, such as those from the Forest Stewardship Council (FSC). The team earned the Innovation point by developing a new, documented framework that linked wood use to climate-resilient forest management — a first in LEED history.
Sustainable Northwest played a crucial role, partnering with the U.S. Bureau of Land Management (BLM), Freres Engineered Wood, and Opsis Architecture to track the wood from the forest to the final installation. The Douglas-fir used for the MPP was harvested from BLM forestland in Oregon’s Willamette Valley as part of a forest restoration project. This project aimed to remove small-diameter trees from an overstocked stand at high risk for catastrophic wildfire. Forest scientists and Sustainable Northwest monitored and documented the restoration efforts.
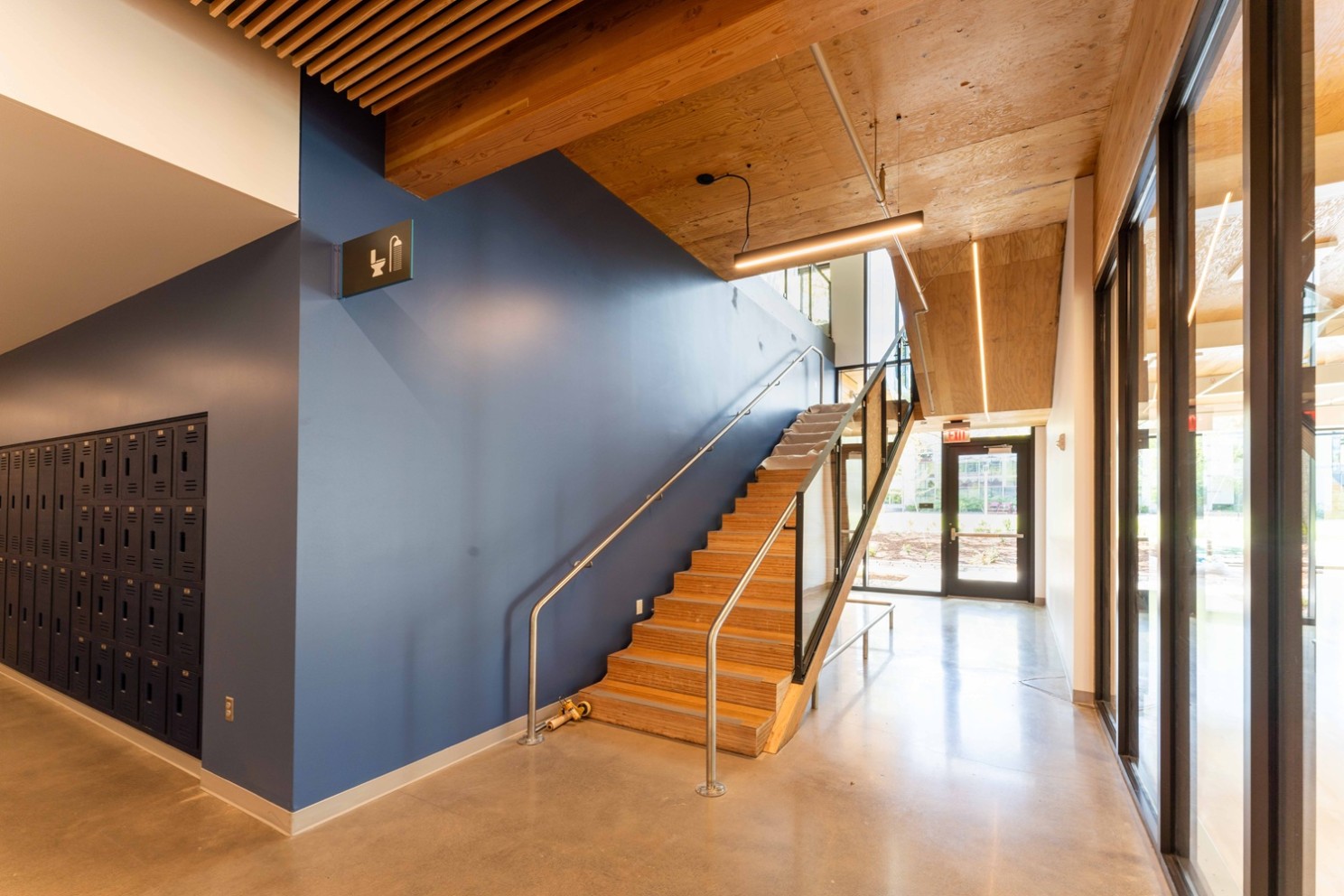
Paul Vanderford, director of green markets for Sustainable Northwest, explained the significance: "We’ve been working since 2019 with leaders in the green building industry to build with and gain credit for using wood products linked to climate-resilient forest stewardship under the LEED and Living Building Challenge certification systems. This innovation point for the Redmond Center gets the entire industry one step closer to being recognized for building with wood that supports healthy forests, a healthy climate, and resilient landscapes". - Sustainable Northwest
Points can be earned by:
- Demonstrating exemplary performance.
- Introducing new sustainability strategies.
- Using materials or methods not yet formally recognized but with strong environmental value.
The innovation point was awarded because Sustainable Northwest facilitated two unique achievements not typically addressed by existing certifications or LEED points:
- Full disclosure of wood sourcing: The project traced the wood from the building back to the specific forest, documenting mill-level log sourcing data.
- Verification of forestry's contribution to landscape resilience and climate values: The project demonstrated that the forestry practices improved forest health, reduced wildfire risk, increased biodiversity, and stored more carbon.
Sustainable Northwest audited the harvest site, noting selective harvesting, healthy riparian areas, species and age diversity (including cedar), and the absence of chemical use – an "excellent example of restoration forestry." This level of transparency and traceability, as Vanderford noted, is a way to "build relationships and elevate the values behind the wood products everyone uses". Furthermore, this system has the potential to advance equity by tracking wood from specific landowners, such as tribes and minority-owned businesses.

Integrated Sustainability Measures
Beyond the use of climate-resilient mass timber, the Redmond Senior Center incorporates a holistic approach to sustainability. The all-electric center is designed to achieve a projected 56.2% reduction in energy costs. An expansive rooftop photovoltaic array will generate renewable energy, aiming to provide 50% of the energy needed to operate the building. Efficient mechanical, plumbing, and electrical systems, as well as high-performance windows and doors, further contribute to energy efficiency. This highly efficient mass timber building is estimated to provide a carbon benefit equivalent to taking 286 cars off the road annually or powering 143 homes for a year.
Structural Ingenuity and Collaboration
The structural design, led by Lund Opsahl, utilized MPP supported by glue-laminated (glulam) beams and columns. The gymnasium features long-span glulam girders supporting the cantilevered walk/jog track, with concealed steel elements strategically incorporated to mitigate vibration. The second-floor weight room and aerobics center include a special multi-layered floor assembly to dampen vibration and reduce sound transmission. Throughout the building, exposed timber necessitated concealed beam-to-beam and beam-to-column connections, resulting in a refined aesthetic that showcases the mass timber elements.
Looking Ahead: A Model for Sustainable Civic Architecture
The Redmond Senior and Community Center is now open. It stands as a testament to what can be achieved when community needs, environmental responsibility, and innovative construction techniques converge. It demonstrates the viability and benefits of using mass timber, particularly wood sourced from climate-resilient forestry practices. This project not only provides a vital community hub but also serves as a model for future sustainable building endeavors, paving the way for greater recognition and adoption of climate-smart wood in the construction industry.
Project Team:
- Owner: City of Redmond
- Design Architect: Opsis Architecture
- Associate Architect: Johnston Architects
- General Contractor: Absher Construction Company
- Mass Timber Supplier: Freres Wood
- Mass Timber Installer: Carpentry Plus, Inc.
- Structural Engineer: Lund Opsahl
- Wood Advisor: Sustainable Northwest
- Hardware Supplier: Simpson Strong-Tie
- Civil Engineer: Herrera Inc.
- Lighting Engineer: LittleFish Lighting
- Landscape Architect: Groundswell Landscape Architecture
- Mechanical, Electrical, Plumbing Engineer, Technology Designer, Energy Modeling/LEED: PAE Consulting Engineers
Frequently Asked Questions (FAQs):
- What is climate-resilient wood? Climate-resilient wood originates from forests that are managed to enhance their health, complexity, and resilience in the face of climate change. These practices often involve selective harvesting, promoting species diversity, and managing for natural disturbances. It's an outcome-based approach that recognizes various forms of forest stewardship.
- Why did the Redmond Senior Center receive a LEED innovation point for its wood use? The U.S. Green Building Council (USGBC) awarded an innovation point because LEED didn't have an existing category for climate-resilient wood. The project was innovative due to the use of mass plywood panels (a newer product), the implementation of climate-resilient forestry practices exceeding standard sustainable harvesting, and the unique tracking and verification of the wood's origin and its contribution to forest health.
- Where did the mass timber for the Redmond Senior Center come from? The Douglas-fir used to create the Mass Plywood Panels was harvested from Bureau of Land Management (BLM) forestland in Oregon’s Willamette Valley. This harvest was part of a forest restoration project aimed at improving the health and resilience of an overstocked stand.
- How was the sustainability of the wood verified? Sustainable Northwest partnered with the BLM, Freres Engineered Wood, and Opsis Architecture to track the wood's journey. They also audited the harvest site in person, documenting the ecological forestry practices implemented. This documentation was submitted to the LEED review team for verification.
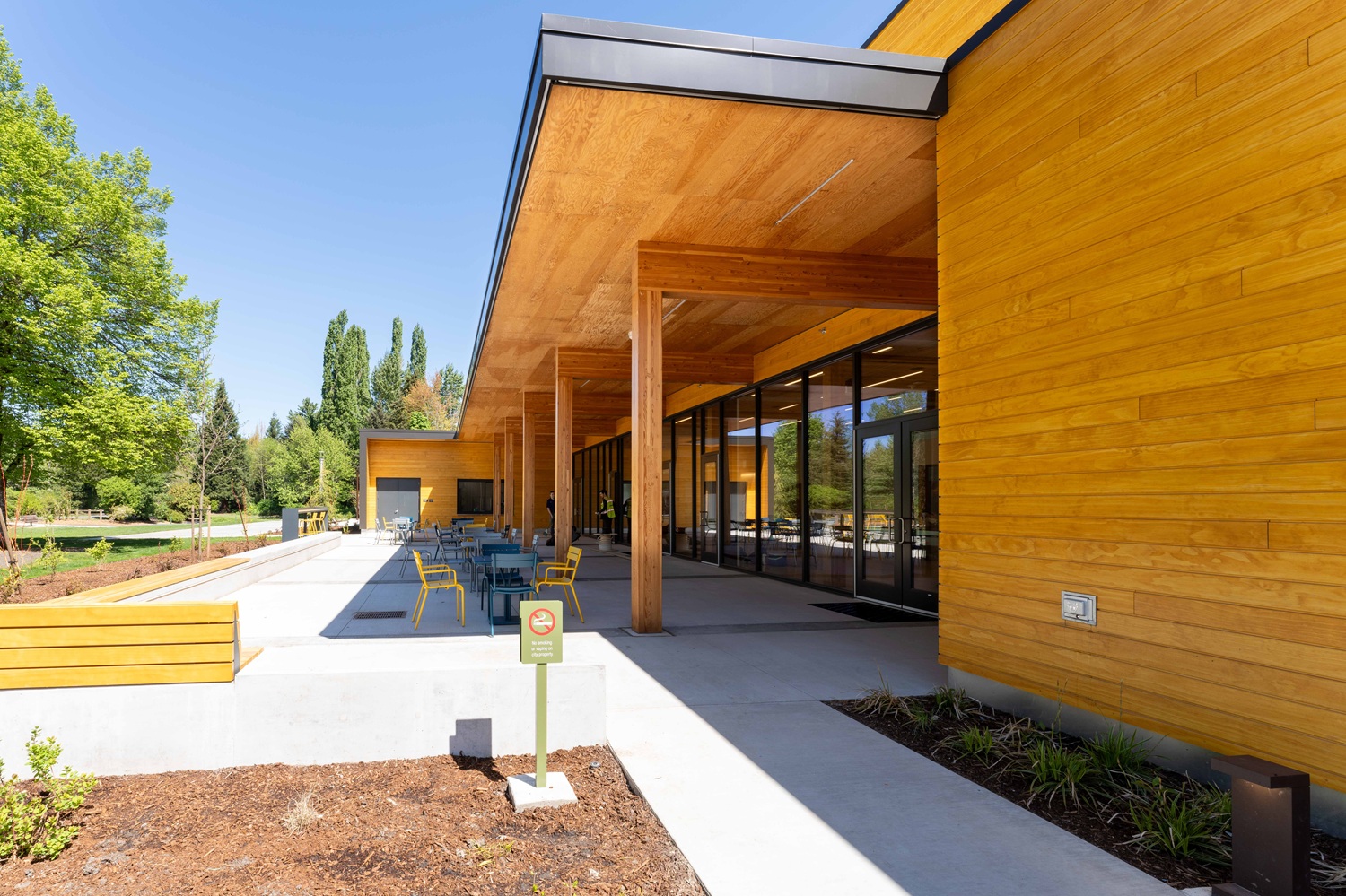
Aura Snowmass: Where Mass Timber Innovation Elevates Alpine Living
Have you ever imagined a luxurious mountain retreat that not only connects you deeply with nature but also treads lightly on the planet? In the heart of Snowmass Base Village, Colorado, a new development has emerged that does just that: Aura Snowmass. This exclusive collection of twenty-one ski-in/ski-out residences isn't just another high-end project; it's a testament to the power of mass timber construction and sustainable design principles, offering a uniquely modern take on traditional alpine architecture.
So, what makes Aura so special? Beyond its prime location flanked by the vast playground of Snowmass Resort, it's the very bones of the buildings – the exposed cross-laminated timber (CLT) structure – that sets it apart. This wasn't a mere aesthetic choice; it was a deliberate decision driven by a commitment to mitigate the effects of new development on climate change and align with sustainable design. As developer Andy Gunion aptly put it, "A mass timber structure turned out to be the perfect fit for the direction we wanted to take on the aesthetics of the project," Andy Gunion said. - East West Partners
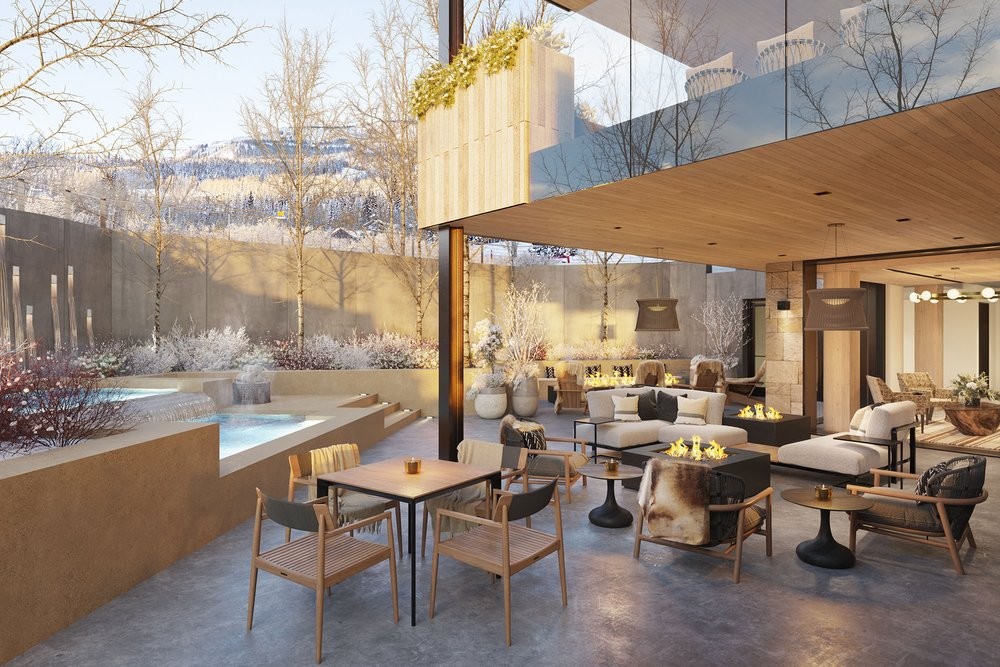
Think about it: traditionally, mountain architecture often conjures images of heavy timber framing. Aura takes this a step further, embracing the engineered beauty of mass timber. This choice not only infuses the interiors with a strong biophilic design expression by leaving much of the timber exposed but also significantly reduces the building’s embodied carbon footprint. Isn't it compelling how a structural material can contribute so directly to environmental responsibility while simultaneously enhancing the living experience?

The stats speak for themselves. Completed in 2023, Aura stands as a five-story multi-family building encompassing an impressive 100,907 square feet. Categorized as a Construction Type III-A building utilizing a Mass Timber building system and Cross-Laminated Timber (CLT), Aura showcases the viability and appeal of this innovative construction method for residential projects.
The decision to use mass timber wasn't just about sustainability; it also played a crucial role in the aesthetic vision for Aura. The exposed CLT creates a sense of warmth and connection to the natural world, perfectly complementing the luxurious finishes and the breathtaking up-mountain and down-valley views. Imagine the feeling of living within a structure where the very material speaks of the forest from which it came.
"We’re thrilled with how the design turned out and how the market is receiving it," Andy Gunion said. - East West Partners
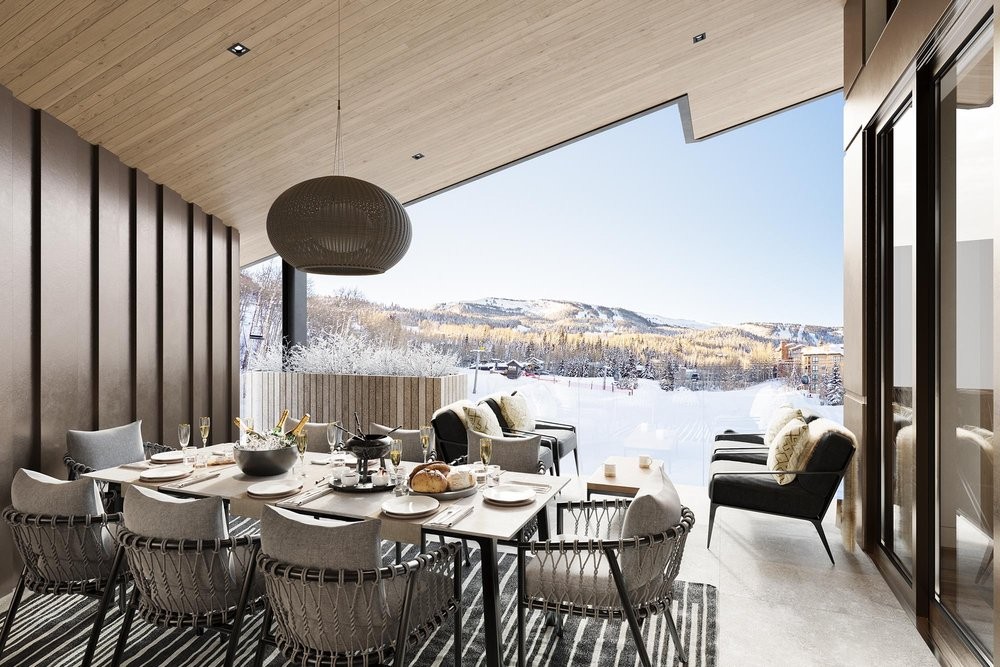
And indeed, the market response was swift, with six of the twenty-one ultra-luxury residences selling in just the first six weeks of sales. This enthusiasm underscores the growing appreciation for both sustainable construction and thoughtful design in high-end residential developments. In fact, Aura has now sold out its residential collection, welcoming twenty-one owner families. This success hints at a broader trend: discerning buyers are increasingly prioritizing homes that reflect their values, including environmental consciousness.
Beyond the innovative use of mass timber, Aura also boasts impressive sustainability credentials. These ultra-efficient, all-electric homes utilize 100% renewable energy sources, resulting in zero ongoing carbon emissions from the building itself. This commitment to minimizing environmental impact extends beyond the structure to the very operation of the residences.
The project team behind Aura brought together a wealth of expertise to bring this vision to life. KL&A Engineers and Builders served as the Structural Engineer, ensuring the integrity and stability of the mass timber structure. The architectural vision was crafted by 4240 Architecture , who skillfully blended modern design with the inherent beauty of the exposed wood. The project was spearheaded by Owner / Developers Andrew Gunion and East West Partners, with Haselden Construction serving as the General Contractor. The collaboration of these talented teams was instrumental in the successful realization of Aura Snowmass.
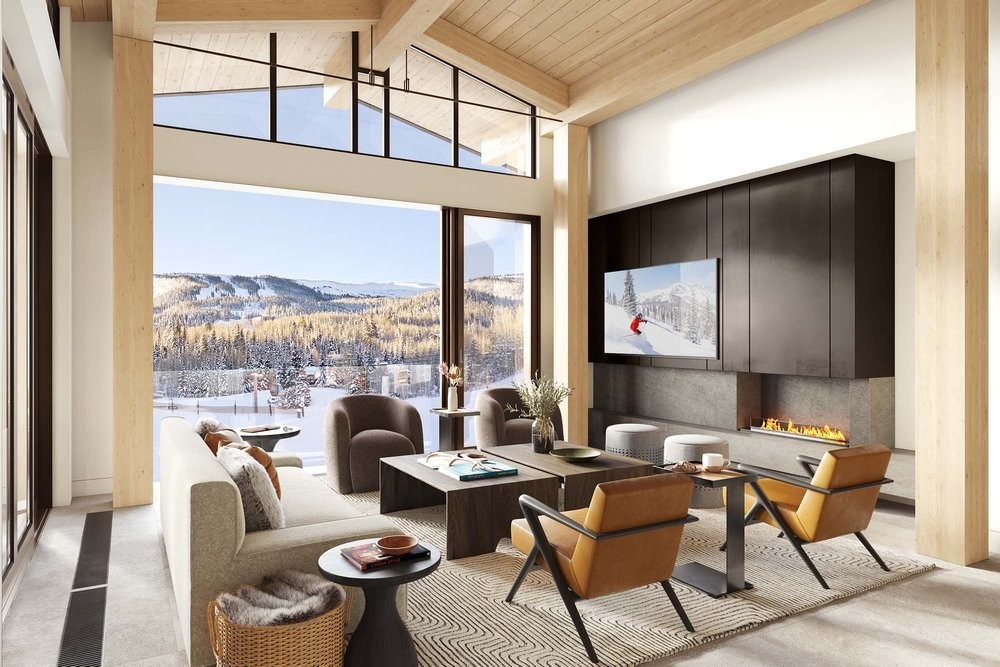
For prospective homeowners, Aura offered more than just stunning architecture and a prime location. The residences were designed with health and wellness in mind, featuring an abundance of natural light, exceptional indoor air quality, and those striking biophilic design elements. The spacious four- and five-bedroom flex floor plans catered to both full-time and second-home mountain living. Inside, gourmet kitchens with high-end Wolf appliances, expansive terraces, and private bathrooms in every bedroom/bunkroom provided the ultimate in comfort and luxury. Two elegant finish packages, Contemporary and Alpine, allowed owners to personalize their spaces.
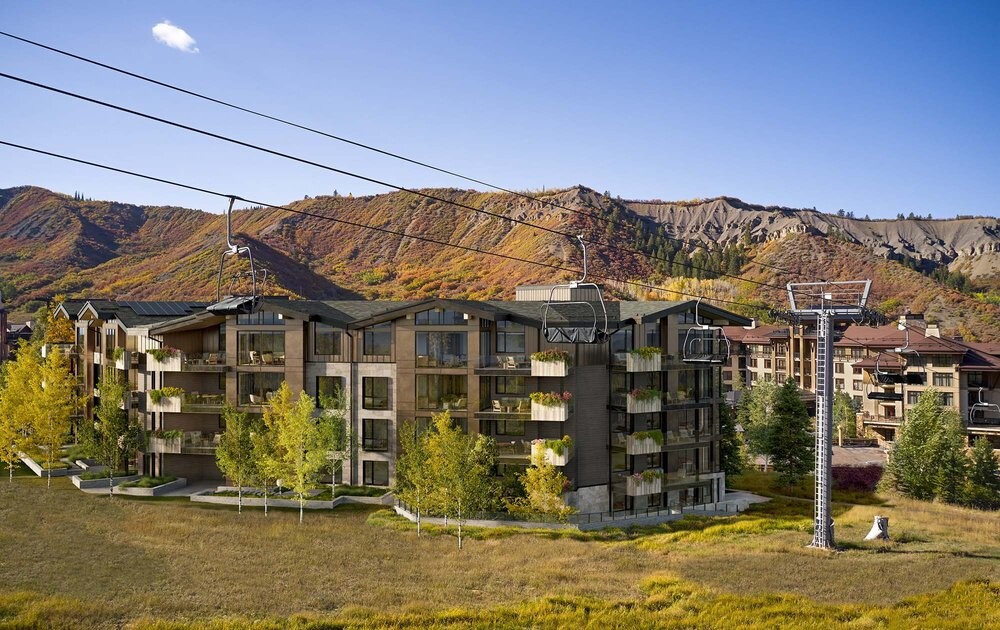
Aura also fostered a strong sense of community and access to the mountain lifestyle. Amenities included private ski lockers (which cleverly transform into bike storage in warmer months), the Aura Lounge for social gatherings, the serene Aura Grotto with spa pools, a private fitness studio, a saltwater Village pool, on-site concierge, and a luge shuttle service.
While Aura Snowmass has achieved a successful sell-out, its legacy serves as an inspiring example for future developments. It demonstrates that luxury, innovative construction, and environmental responsibility can go hand in hand. Projects like Aura are paving the way for a more sustainable and architecturally rich future in the built environment.
Project Team:
Owner / Developer: Andrew Gunion & East West Partners
Architect: 4240 Architecture
Structural Engineer: KL&A Engineers and Builders
General Contractor: Haselden Construction
Frequently Asked Questions (FAQs):
- What is mass timber construction? Mass timber refers to a category of engineered wood products made by binding together multiple solid wood laminations, dimensions, or strands using adhesives, fasteners, or friction. Examples include cross-laminated timber (CLT), glued laminated timber (glulam), nail-laminated timber (NLT), and dowel-laminated timber (DLT). These materials offer high strength and stability, making them suitable for various structural applications.
- Why was mass timber chosen for the Aura Snowmass project? Mass timber was chosen for Aura Snowmass in part to help mitigate the effects of new development on climate change and because it aligns with principles of sustainable design. Additionally, it provided the desired aesthetic for a strong biophilic design expression and a uniquely modern take on traditional alpine architecture.
- What are the key sustainability features of Aura Snowmass? Aura Snowmass features a mass timber structure that significantly reduces the building’s embodied carbon footprint. The homes are ultra-efficient and all-electric, using 100% renewable energy sources, resulting in zero ongoing carbon emissions from the building itself.
- What types of residences were offered at Aura Snowmass? Aura Snowmass offered an exclusive collection of twenty-one ski-in/ski-out residences, featuring spacious four- and five-bedroom flex floor plans.
- Who were the key companies involved in the Aura Snowmass project? Key companies involved in the Aura Snowmass project included East West Partners (Owner / Developer), 4240 Architecture (Architect), KL&A Engineers and Builders (Structural Engineer), and Haselden Construction (General Contractor).
👋 If you enjoyed this - you can...
Level Up Your Mass Timber IQ & Stay Up to Date on Industry Trends
with original reporting, people you should know & must-read headlines direct to your inbox!
Click Here to Subscribe to the Mass Timber Times
And if YOU want to join a community of mass timber experts IN PERSON for advanced education, project collaboration and networking events that you actually want to attend - check out the Mass Timber Group Summit below...
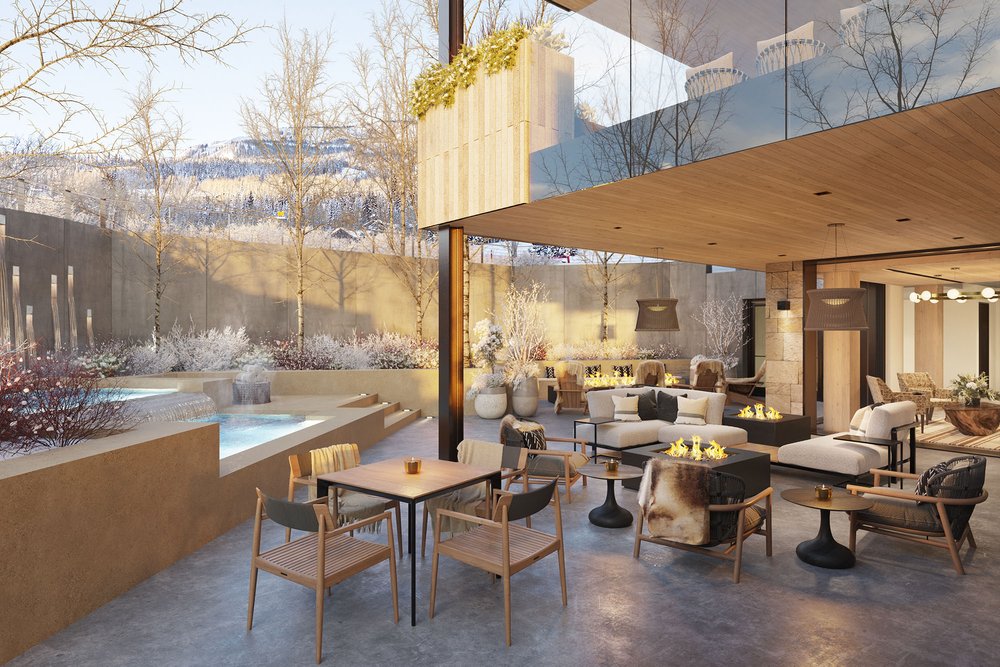
Building Mass Timber for DeafSpace: Inside the Expansion at the Washington School for the Deaf, Divine Academic & Hunter Gymnasium
Have you ever walked into a space and instantly felt that it was designed with you in mind? That’s the feeling echoing through the halls of the newly expanded Washington Center for Deaf and Hard of Hearing Youth (CDHY) aka Washington School for the Deaf, Divine Academic & Hunter Gymnasium in Vancouver, Washington. This isn't just another school construction project; it's a testament to thoughtful design, deep collaboration, and a profound commitment to creating an optimal learning environment for deaf and hard of hearing students.
For the students and staff at CDHY’s Washington School for the Deaf (WSD), the completion of the Divine Academic Building and the Hunter Physical Education Building marks a significant milestone. As the state’s only residential American Sign Language (ASL) – English bilingual school for deaf and hard of hearing students, CDHY plays a vital role in ensuring these young individuals reach their full potential. The expansion, a two-year endeavor, brings much-needed modern facilities to a campus that hadn't seen new classroom construction since 1971.
So, what makes this project so special for the architects, engineers, and construction experts involved? It’s the intentional integration of DeafSpace principles, the innovative use of mass timber, and the unwavering focus on the unique sensory and communication needs of the students.
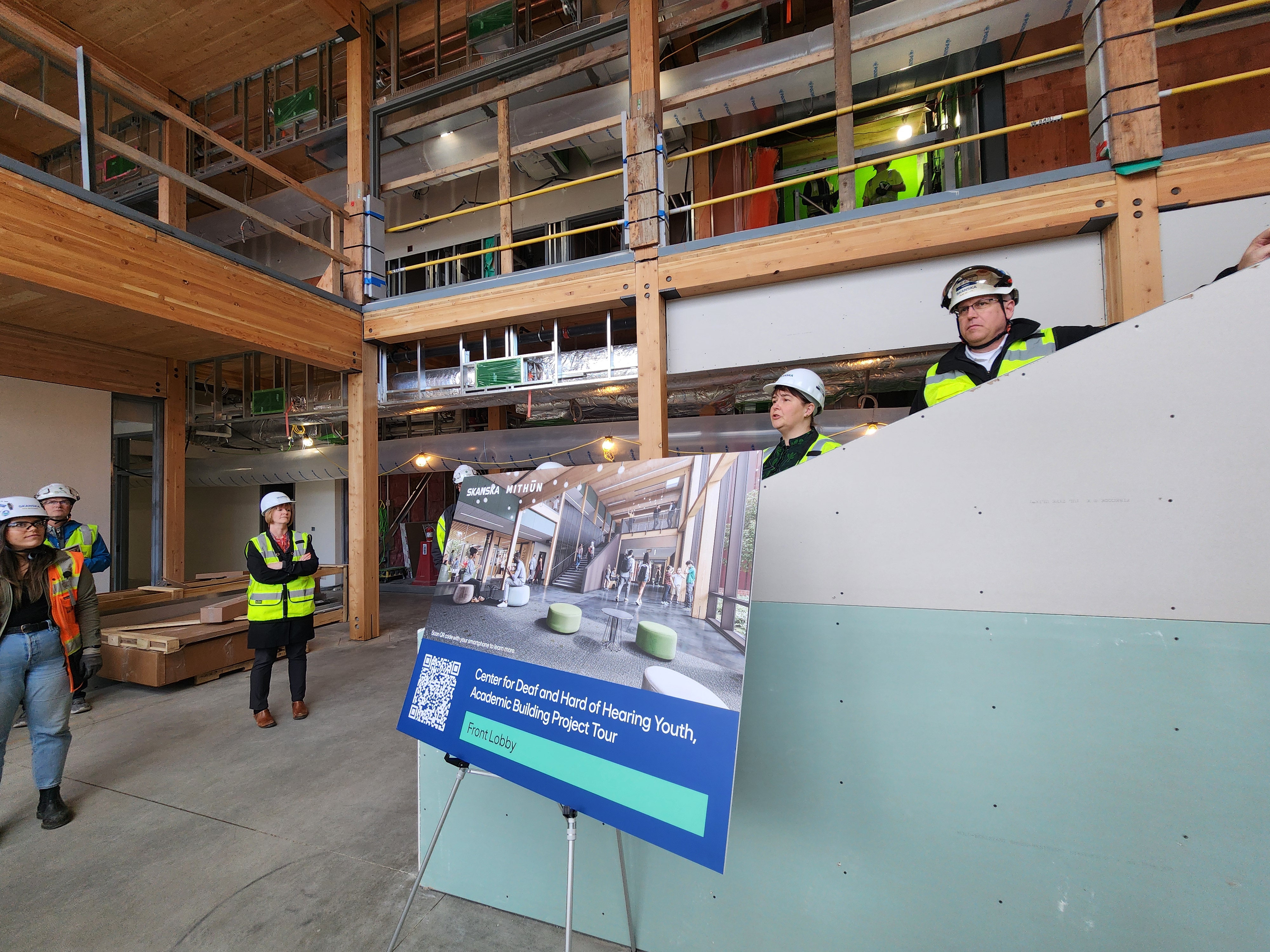
From Vision to Reality
Bringing this vision to life was a collaborative effort spearheaded by Skanska, a leading construction and development firm, and Mithun, their design partner. The Washington State Department of Enterprise Services (DES) provided project management, ensuring the project aligned with the state’s goals. But perhaps the most crucial aspect of the process was the deep engagement with the CDHY community itself.
Trevor Wyckoff, Senior Vice President and Account Manager at Skanska, emphasized this collaborative spirit, stating, “We wanted to be part of the Center for Deaf and Hard of Hearing Youth project because of the positive impact it would have on the students, families, staff, and entire community”. He further noted, “We collaborated with Mithun, the Department of Enterprise Services, and CDHY, to engage students and staff throughout the design and building process, creating a sense of ownership and excitement for the new buildings”. This wasn't just about constructing buildings; it was about co-creating spaces that truly served their users.
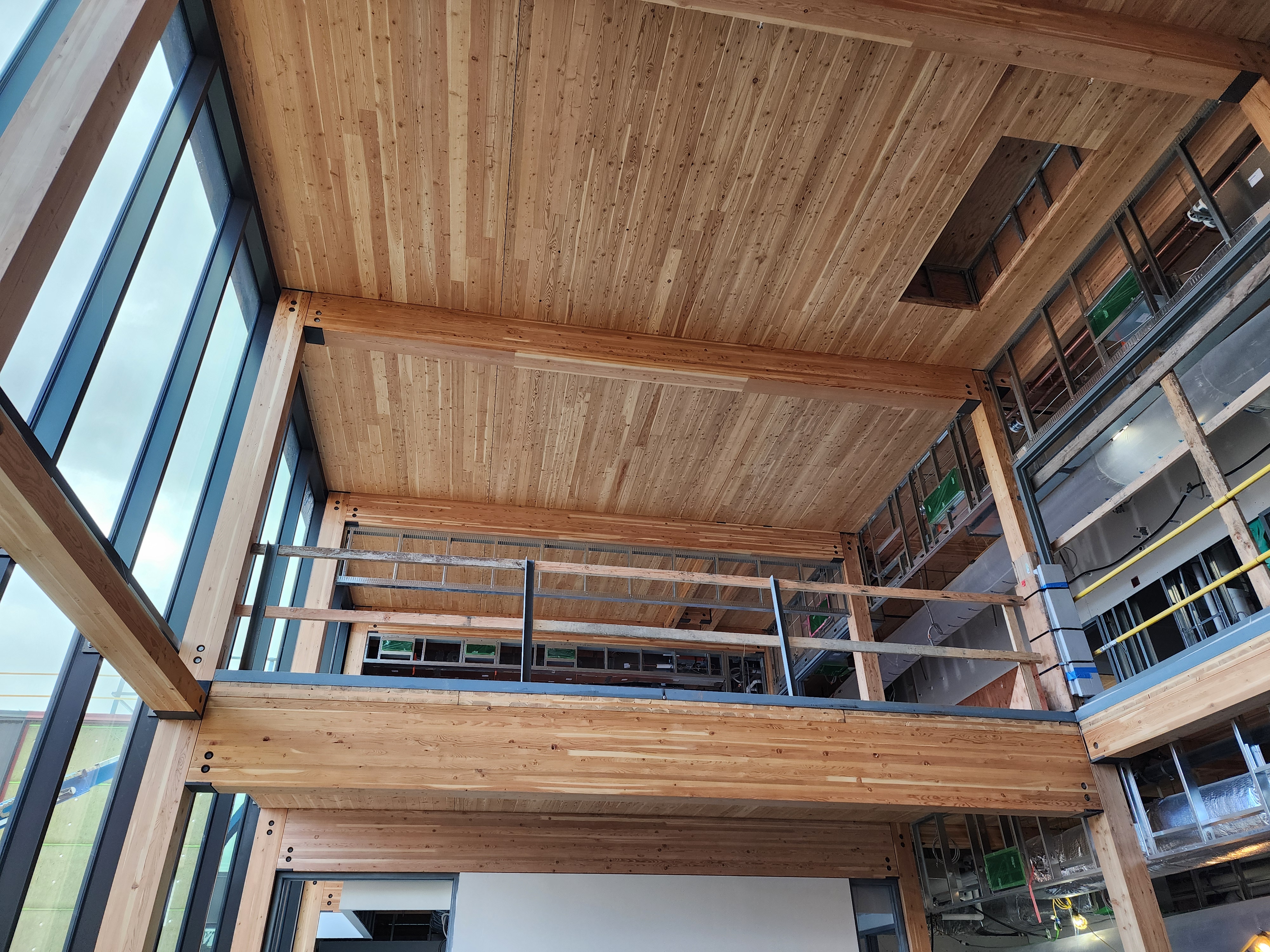
Mithun partner JoAnn Hindmarsh Wilcox echoed this sentiment, saying, “Our team is honored to be conversation partners with the Washington School for the Deaf community”. She highlighted the core principle guiding the design: “Understanding the importance of maintaining Deaf culture, and ensuring students have full access to information, become our collective hearthstone as we worked together to consider every aspect of the Deaf experience and tune the buildings accordingly”.
Even beyond the core team, specialist expertise played a vital role. Consultants Hansel Bauman and Robert T. Sirvage brought their knowledge of DeafSpace Guidelines to inform every aspect of the design and construction.
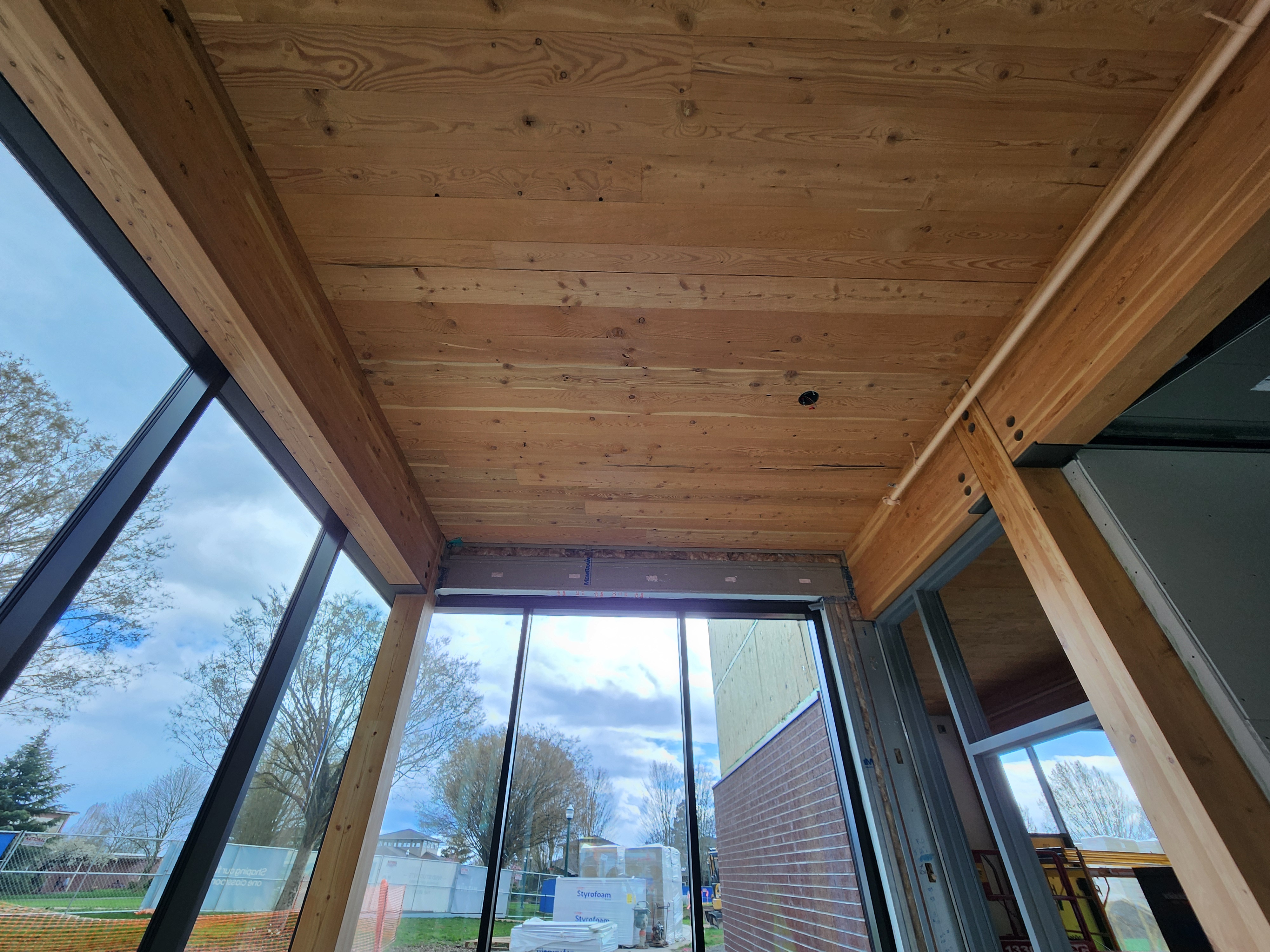
DeafSpace and Sensory Sensitivity
What exactly are DeafSpace Guidelines? They are a set of design principles that address the unique spatial and sensory needs of deaf and hard of hearing individuals. Alan Halleck, Skanska project executive, even studied ASL to better understand these guidelines and the community’s needs. As Halleck explained, these principles require that “multi-purpose spaces are designed to enhance American Sign Language (ASL)-English bilingual instructional practices through improved technology infrastructure and incorporating DeafSpace design principles, including sensory reach, space and proximity, mobility, light and color, and acoustics”.
Shauna Bilyeu, executive director at CDHY, underscored the importance of these considerations: “This expansion means two brand new and much-needed spaces for improved learning and athletics in this unique student environment,” she said. She further elaborated on the tangible design outcomes, mentioning “wider-set hallways for active ASL (American Sign Language) communication and so much other care and concern for the needs of our unique community”. Wider hallways allow students to walk side-by-side while signing, maintaining visual communication.
The design also considered acoustic vibration as a communication method, with floors accommodating these vibrations. Natural lighting was another key element, with extensive use of large windows – often with low-glare coatings to prevent eye strain. As Bilyeu noted, the partners “cared so deeply about getting it right”.
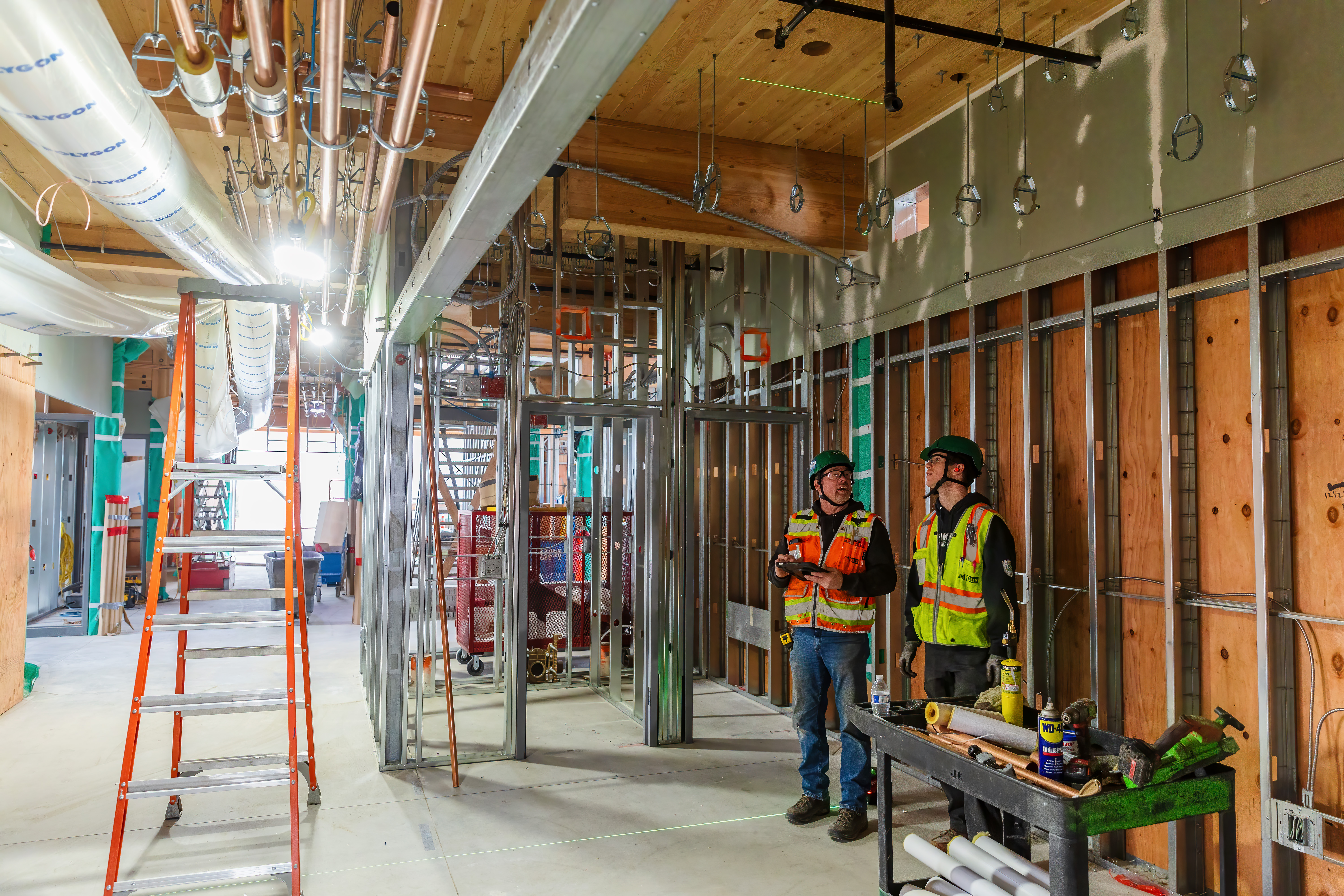
The Beauty and Benefits of Mass Timber
Beyond the DeafSpace considerations, the project stands out for its innovative use of mass timber. The Divine Academic Hall incorporates glue-laminated timber for columns and beams, and three-ply cross-laminated timber (CLT) for the roof structure and floors. According to Whitney Geier, Director of Marketing at Skanska, the mass timber species for both glulam and CLT is Douglas-Fir-Larch, harvested from forests in the Kootenays in British Columbia. The project utilized 131 cubic meters of glulam (a running length of 5770 feet) and 308 cubic meters of CLT (roughly 10,876 cubic feet).
This choice of material wasn't arbitrary. Informed by Mithun’s Building Better Schools R+D study, the mass timber system proved to be cost-competitive with traditional building methods and resulted in a ratio of less than .50 cubic feet of wood fiber per gross square foot of building area, below industry standard.
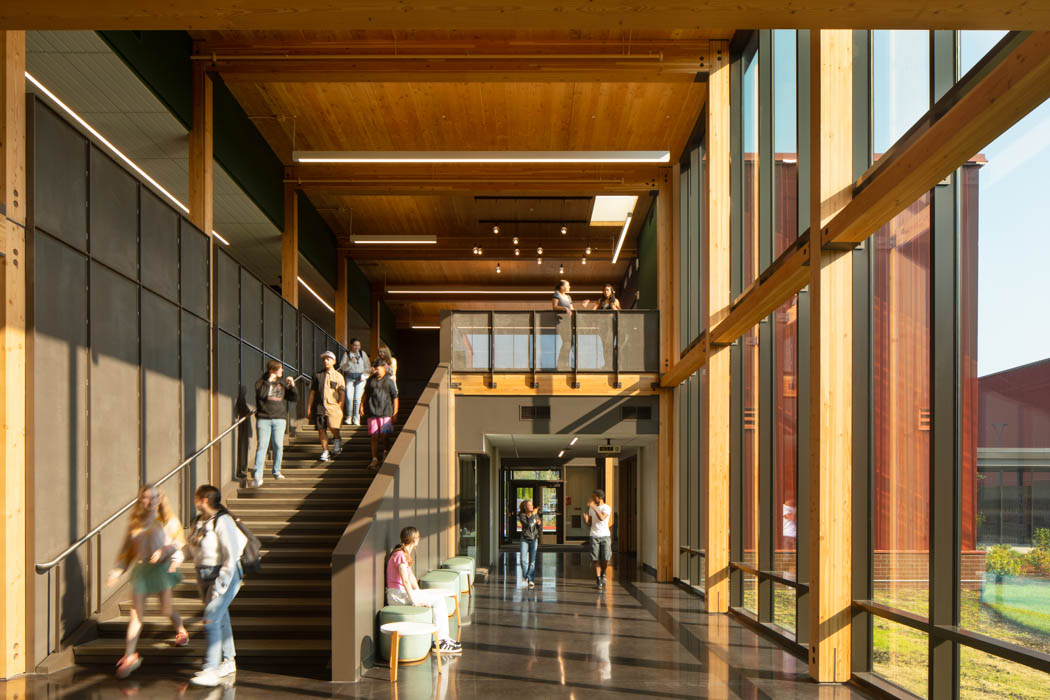
But the benefits extended beyond cost. As noted, Kalesnikoff said “the mass timber design was optimized to bring biophilic benefits to student well-being and learning outcomes.” Furthermore, it helps make the most of acoustic vibrations to extend occupants’ sensory reach, a crucial element for deaf individuals who rely heavily on visual and tactile cues.
Shauna Bilyeu expressed her personal connection to the material: “Many of our students live on campus from Sunday through Friday, so it was important that the school feel like home. I wanted buildings that were happy and full of light. To me, that meant mass timber”. The use of wood also pays homage to the school's history, connecting back to a demolished campus landmark, the Red Barn, which held deep community significance.
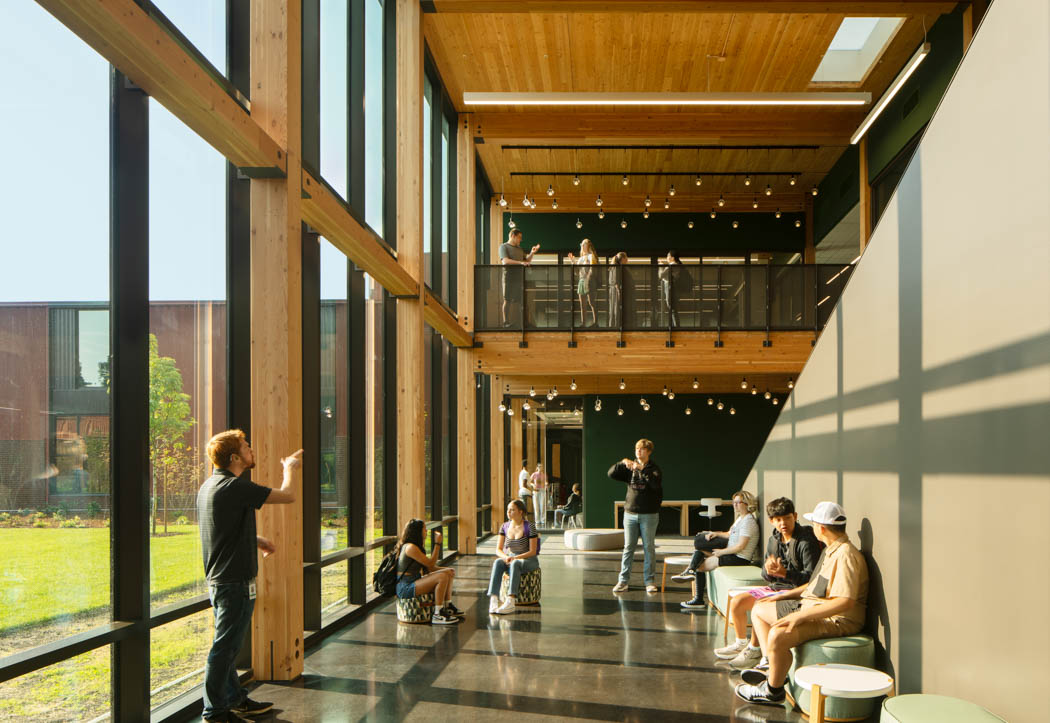
Navigating Challenges and Achieving Excellence
No construction project is without its hurdles. Abe Ott, Director of Marketing & Proposals at JH Kelly, the design/build MEP trade partner said "there is a critical need for early detailing and coordination due to the custom fabrication and lead times of the CLT components.” He emphasized the close collaboration between the electrical, mechanical, and plumbing teams to maximize space within the mass timber structure and preserve its aesthetic.
Ott also pointed out the challenges posed by the Pacific Northwest weather. “As the building was erected during rain and snow events, the mass timber elements ended up pulling in moisture,” he explained. To mitigate this, heaters and dehumidifiers were used to dry the wood as the building envelope was completed.
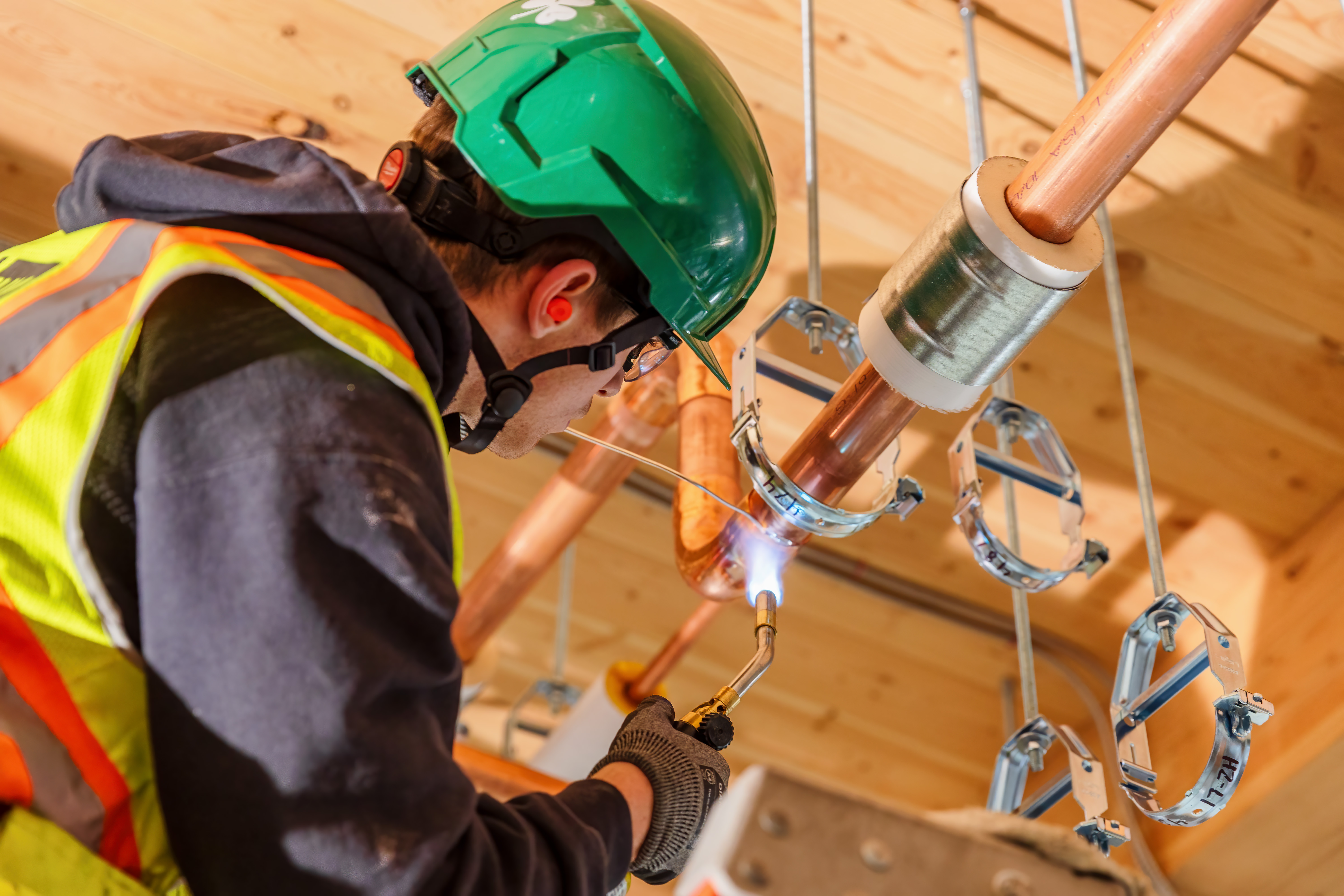
Whitney Geier from Skanska shared unique challenges encountered during the design phase. Initially, mass timber wasn't part of the proposed design. The subsequent addition required a new builder’s risk insurance policy with a significantly higher premium. Through collaboration between Skanska, PCS Structural Solutions (the engineer), and Mithun, they submitted a detailed risk mitigation application, successfully negotiating the insurance fee down.
This project also had exposed conduit on the surface of the floor deck that needed to be addressed. “Using USG's solution, this installation allowed for the exposed conduits to be encapsulated in the first layer of poured gypsum flooring rather than routing out the CLT deck to bury the conduit. This provided an efficient solution for hiding the conduit while saving both time and labor. The applicator, Ultra Quiet Floors, assisted with installation of the USG Levelrock® Brand gypsum underlayment and sound mat on the project, drawing on their extensive knowledge of installing such systems in mass timber construction.” - Jennifer Chambers, USG Specifications Manager
The project is on track to achieve LEED Gold certification, demonstrating a commitment to sustainability. According to Whitney Geier, the project has an embodied carbon emission of 88.5 kgCO2e/m2, exceeding most benchmark projects.
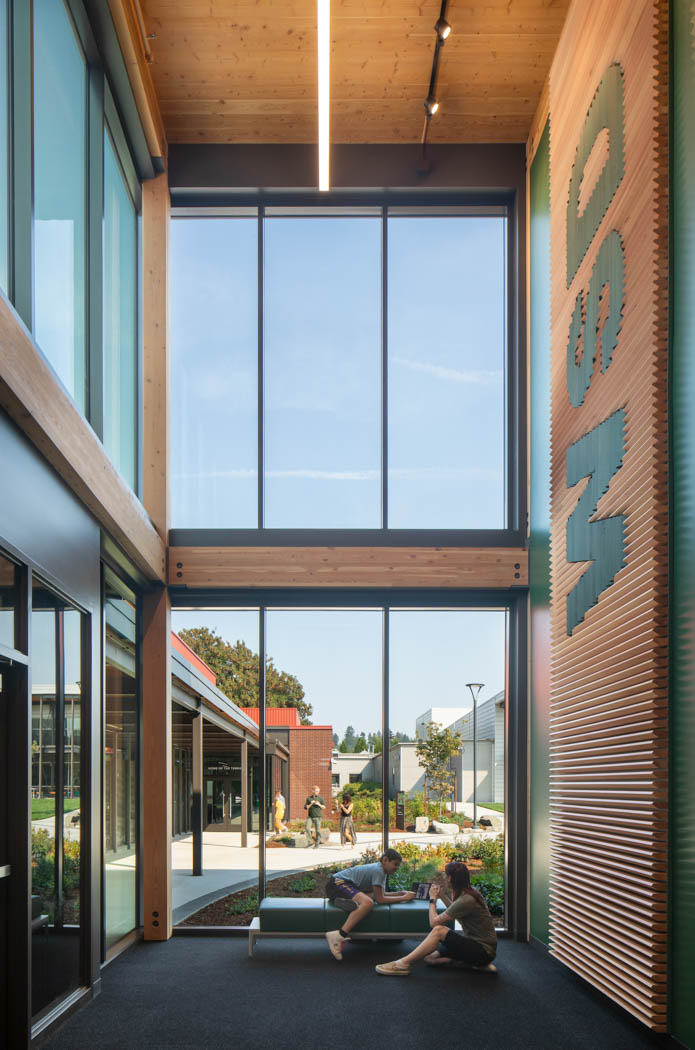
A Legacy of Care and Innovation
The expanded CDHY campus isn't just about new buildings; it's about creating a holistic environment that fosters linguistic, cognitive, social, and emotional development while honoring Deaf culture. The new 35,000-square-foot Divine Academic Building includes innovative classrooms and a media center, while the 15,000-square-foot Hunter Gymnasium provides a purpose-designed space for physical education. A sensory-focused and accessible playground, a secure walkway connecting the buildings, and an improved parking area further enhance the campus. A new outdoor field is slated for completion in Spring 2025.
As Washington Governor Jay Inslee remarked at the ribbon-cutting ceremony, “We are witnessing how partners in funding, design and construction have modeled this innovative solution for this special needs population. Washington state is proud to support the needs of deaf and hard of hearing youth”. - Skanska
For the students, families, and staff at CDHY, this expansion represents more than just new facilities – it signifies a renewed commitment to their unique needs and a brighter future for generations to come. As Shauna Bilyeu aptly stated, “We now have a beautiful school that is unique to our community. It’s sustainable and something that the larger metro Vancouver area is proud of”.
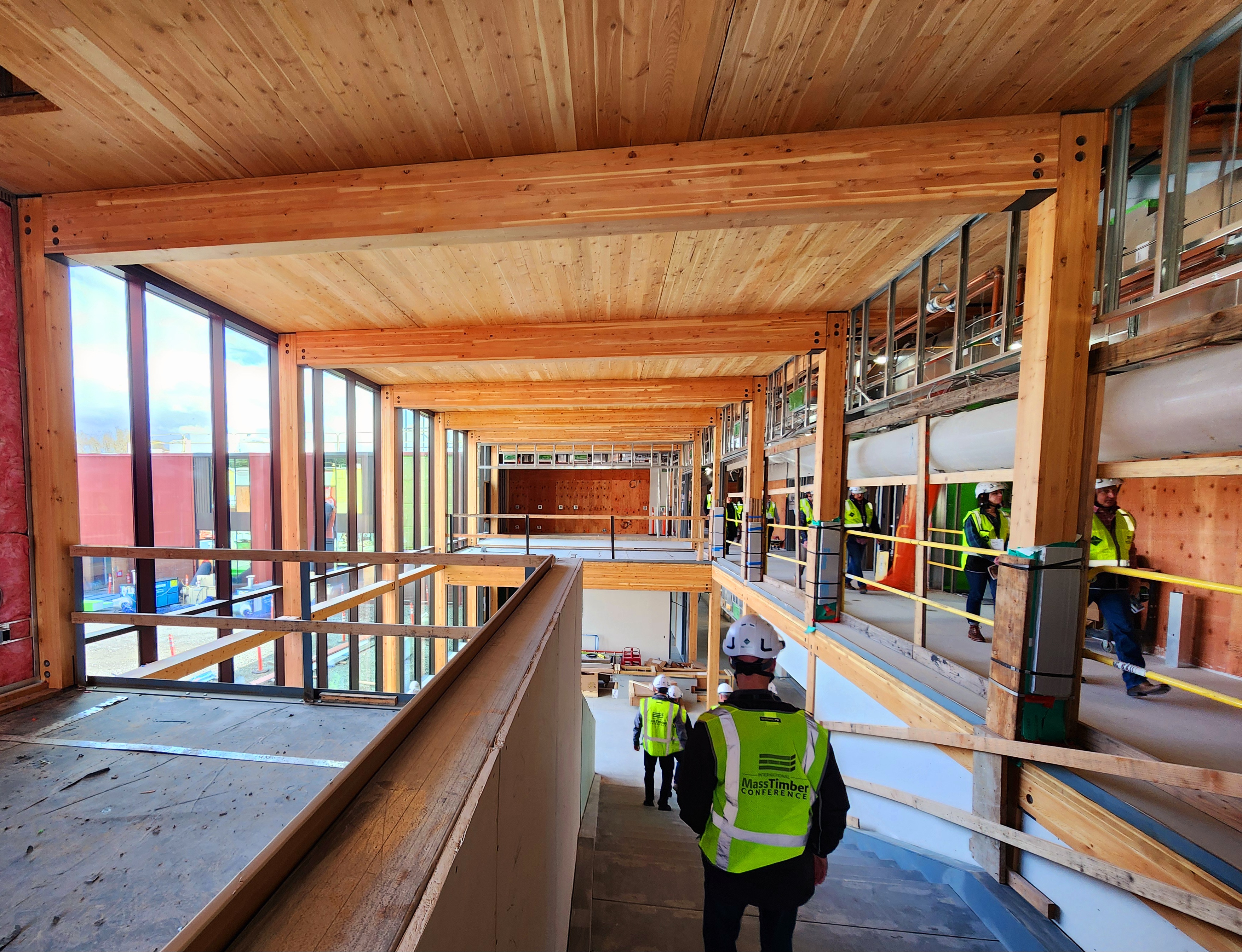
Project Team:
- Owner: Center for Deaf and Hard of Hearing Youth (CDHY)
- Project Management: Washington State Department of Enterprise Services (DES)
- Progressive Design-Build Lead & General Contractor/Construction Manager: Skanska
- Architecture, Landscape, and Interior Design: Mithun
- DeafSpace Consultants: Hansel Bauman and Robert T. Sirvage
- Structural Engineer: PCS Structural Solutions
- MEP and Technology: Glumac, JH Kelly, LLC
- Civil Engineer: Harper Houf Peterson Righellis
- Fire Protection: McKinstry
- Mass Timber Supplier: Kalesnikoff Mass Timber
- Gypsum Underlayment and Sound Mat: USG
Photography: Candra Burns , Lara Swimmer, and Abe Ott
Candra's Editor Note: Washington State is leveling up the accommodation in old spaces. WOW!! Growing up in a place with this kind of history and beauty has made me fortunate. I ended up with an owner trained Service Dog later in life who is now retired. I understand the sensory needs of people and had to come see this project while under construction. I knew that exposed mass timber and the windows would make light everywhere in the room appear bright for students to navigate better. The stairs are wide enough for students to do sign language and walk at the same time with multiple people at once. I accommodated myself my whole life for sensory needs and this is the best school for future needs of those with the visual, tactile, and spatial needs.
Frequently Asked Questions:
1. What are DeafSpace Guidelines, and how were they incorporated into the CDHY expansion project? DeafSpace Guidelines are design principles focused on the visual, tactile, and spatial needs of deaf and hard of hearing individuals. They were incorporated throughout the design process through collaboration with DeafSpace consultants, resulting in wider hallways for signing, strategic use of lighting, and consideration of acoustic vibrations.
2. Why was mass timber chosen as a primary building material for the Divine Academic Hall? Mass timber was chosen for its cost-competitiveness, biophilic benefits promoting well-being, its ability to enhance sensory reach through acoustic vibrations, its aesthetic appeal in creating a home-like environment, and its lower embodied carbon footprint, aligning with sustainability goals.
3. What were some of the unique challenges faced during the construction of this project? Unique challenges included the need for meticulous early coordination due to the prefabricated nature of the CLT, managing moisture in the mass timber during rainy weather, and addressing unforeseen structural conditions related to an existing basement.
4. How did the design team ensure the new facilities met the specific educational and cultural needs of the deaf and hard of hearing students? The design team engaged students and staff throughout the design process, conducted deaf-led workshops, and prioritized visual access and ASL-English bilingual instructional practices through the incorporation of DeafSpace principles and improved technology infrastructure.
5. What is the expected sustainability performance of the new CDHY facilities? The project is on track to achieve LEED Gold certification and demonstrates strong sustainability performance through the use of mass timber, resulting in an embodied carbon emission of 88.5 kgCO2e/m2, which exceeds most benchmark projects.
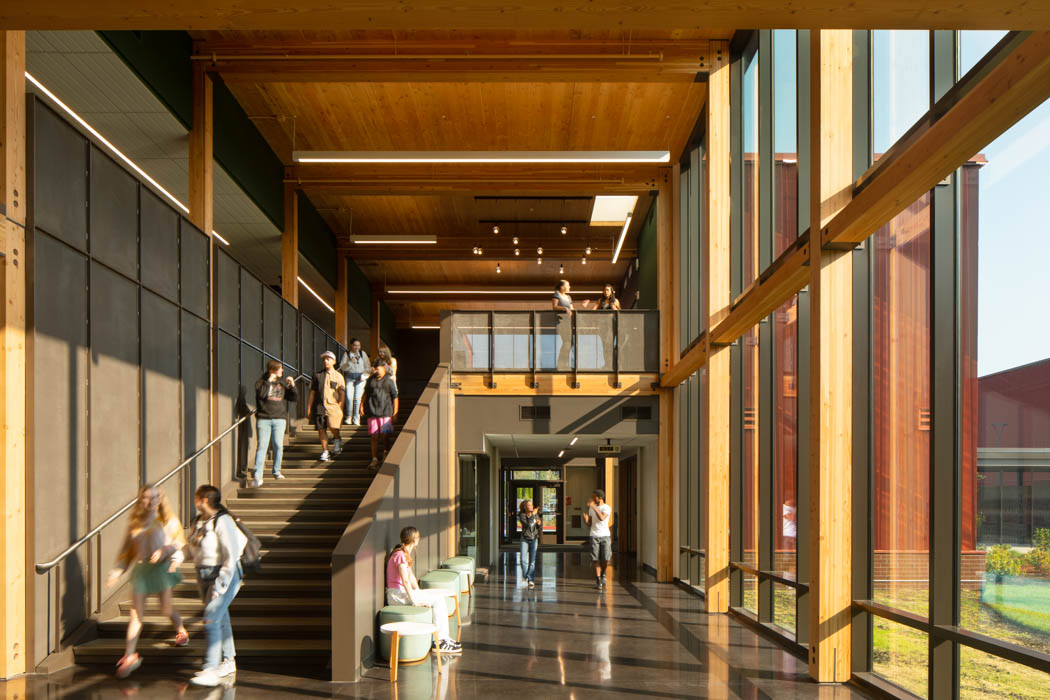
Size - The 2nd Mass Timber Myth That Needs to Die
Here's the 2nd of five myths we hear most often — and why they need to go.
(If you missed the first - you can learn about it here)
At the 2025 Mass Timber Group Summit, we’re putting these myths to rest for good — backed by real project data, expert insights, and lessons learned directly from teams in the field.
✅ Myth 2: Mass Timber is Only for Large Buildings
For years, mass timber was seen as a material reserved for bold, headline-grabbing projects — 10+ story towers in urban cores, university innovation hubs, and flagship public buildings. But that’s outdated thinking. Mass timber’s versatility isn’t just for the skyline — it’s showing up in modular homes, workforce housing, ADUs, and even single-family projects across North America.
Matt’s Place: Modular Timber Homes for Accessibility & Sustainability
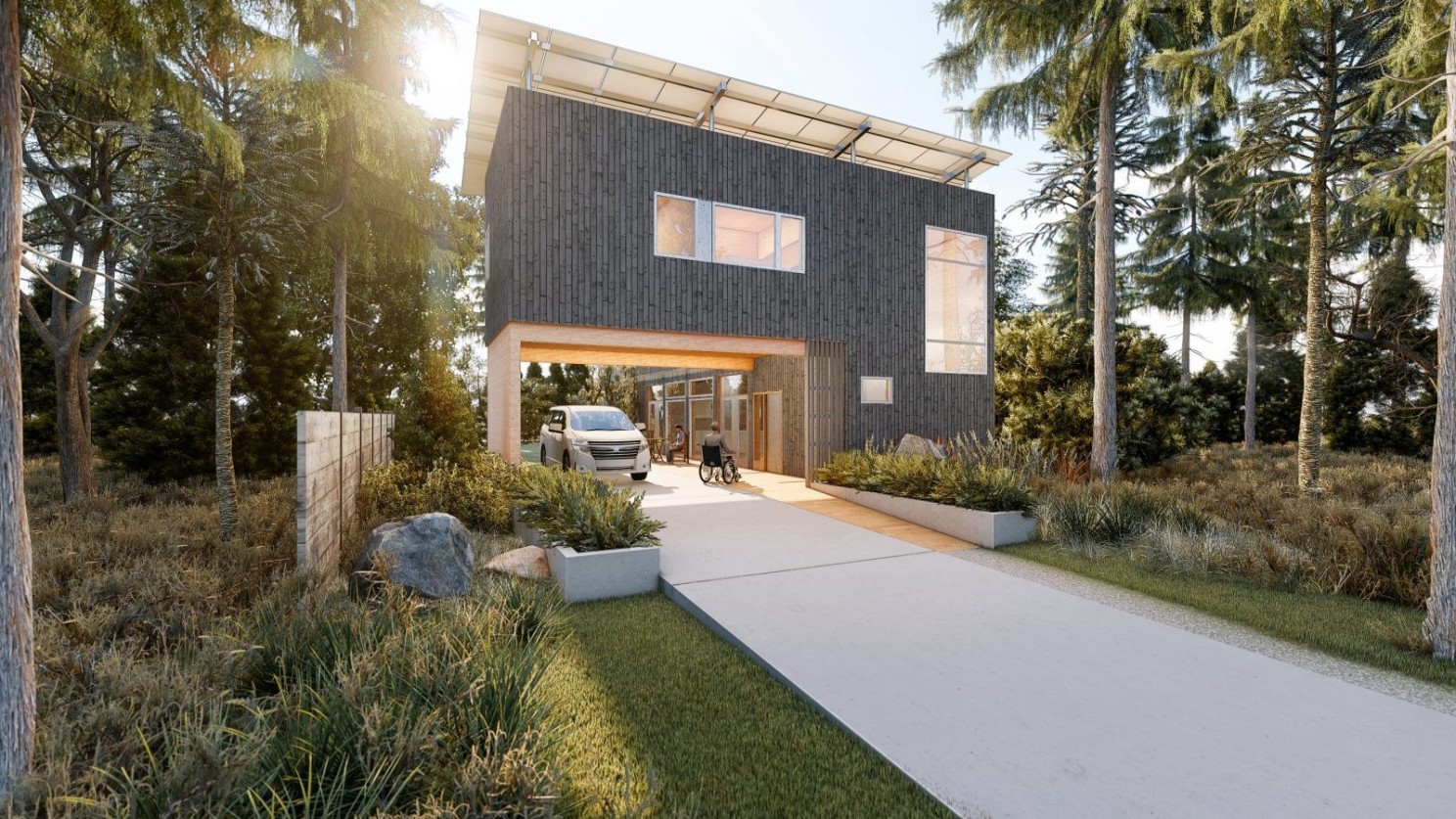
The Matt’s Place project offers one of the clearest examples of mass timber breaking into smaller-scale, high-performance housing. Conceived as an accessible, climate-resilient home for people living with ALS, Matt’s Place uses prefabricated mass timber panels & modular components to accelerate construction, enhance durability, and significantly improve energy performance.
- Mass timber panels form the building’s shell, reducing framing time to just a few days.
- Panels are pre-cut and arrive ready for assembly, minimizing on-site waste and labor.
- Integrated mechanical chases and pre-installed systems (like plumbing and electrical components) further speed up construction.
This project is now in its third iteration — proof that the system works and can be replicated at scale for affordable and accessible housing.
Alex Zink, AIA & Brian Court from The Miller Hull Partnership, LLP, DCI Engineers, and Andy Barrett will be helping you understand how to apply the same lessons from Matt's place to you own projects in Denver this summer (more on that later).
Timber Age Systems: Mass Timber for Local, Attainable Homes
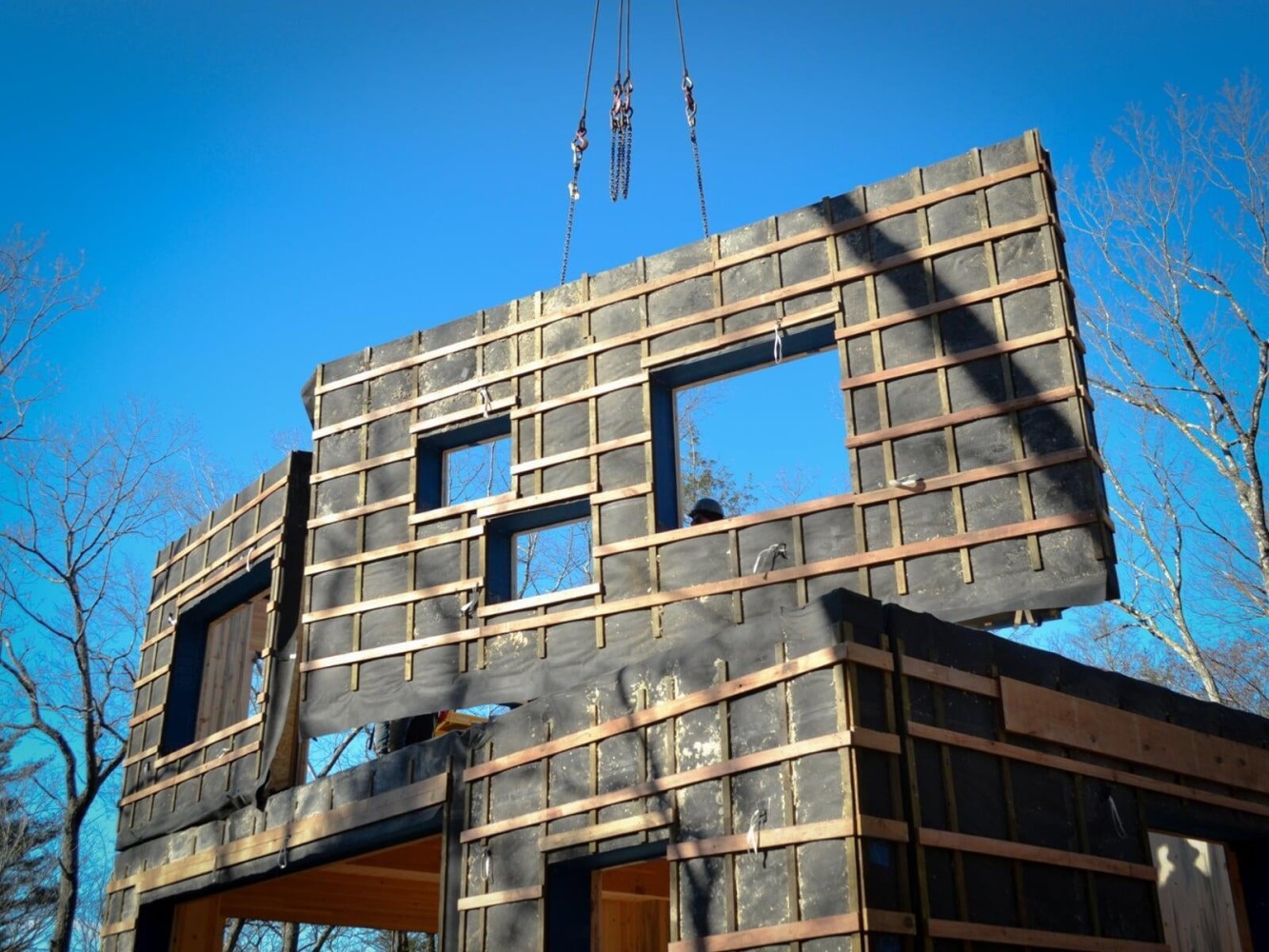
In Durango, Colorado, Kyle Hanson and the Timber Age™ team is proving that mass timber isn’t just for big cities or luxury projects. Their panelized mass timber system is designed specifically for attainable, high-performance housing. What sets them apart:
- Walls built from locally harvested Ponderosa Pine — sourced locally.
- Panels arrive pre-insulated (R-52), air-sealed, and ready for cladding — dramatically reducing site labor.
- Typical shell installation time: 2-3 days for a 1,000 SF home.
- Price point for the structural shell: as low as $85 per square foot — directly competitive with traditional high-performance framing.
This approach solves several challenges at once: it boosts local forestry economies, reduces embodied carbon, supports workforce housing, and makes passive house-level performance attainable. Timber Age is actively delivering homes in Colorado and beyond — proving mass timber works at residential scale.
The Takeaway
The truth is, mass timber isn’t inherently a “big building” material. It’s a high-performance, modular-friendly, design-flexible system that scales up or down depending on the project needs. What’s been holding mass timber back in residential and small-scale markets isn’t the material itself — it’s outdated assumptions perpetuated by some members of the design and construction community.
With teams like Timber Age and projects like Matt’s Place leading the charge — there’s no reason to leave mass timber off the table for homes, ADUs, or small commercial buildings.
That’s exactly what we’ll break down at the 2025 Mass Timber Group Summit—real-world numbers, hard-earned lessons, direct from the teams proving mass timber works at any scale.
👉 Secure Your Spot at the Summit
Up Next: Myth 3 - You Already Need to Be a Specialist to Design & Build with Mass Timber
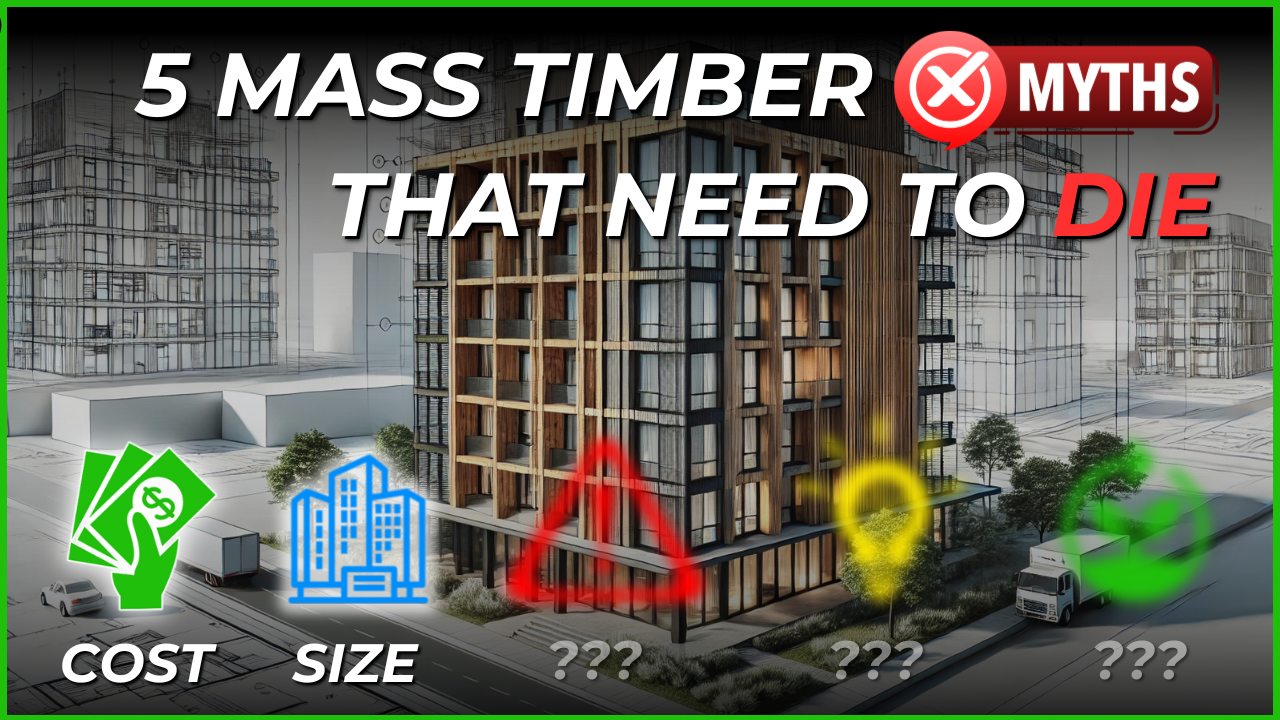
5 Mass Timber Myths That Need to Die (1/5)
Mass timber is growing fast — but outdated beliefs are still slowing down projects, driving up costs, and creating hesitation with clients. Some AEC teams are holding onto myths that don’t match today’s reality.
Here’s the 1st of 5 myths we hear most often — and why they need to go.
At the 2025 Mass Timber Group Summit, we’re putting these myths to rest for good — backed by real project data, expert insights, and lessons learned directly from teams in the field.
✅ Myth 1: Mass Timber is ALWAYS More Expensive
This myth refuses to die — and it’s costing teams real opportunities.
On paper, direct material costs for mass timber can appear higher than steel or concrete. That’s where too many teams stop the analysis. But the smartest project teams — the ones actively delivering successful mass timber buildings — know the real math happens at the total project level, not just the materials line item.
Case in Point: 1510 Webster
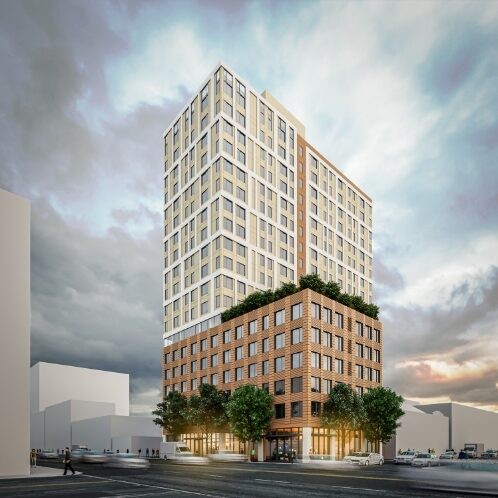
Take 1510 Webster in Oakland, CA — a 19-storey Type IV-A building and the world’s first high-rise to use point-supported Mass Plywood Panels (MPP) from Freres Wood. After full cost comparisons with previously designed buildings in their portfolio, the developer oWOW, found that mass timber could match or beat alternative materials - to the tune of $30 Million— without compromising performance.
Where did that competitive edge come from?
✅ Lighter Structure: Mass timber’s strength-to-weight ratio reduced foundation size, excavation work, and concrete costs.
✅ Faster Assembly: The 40' x 10' MPP panels used were being installed at a rate of 1 every 15 minutes - or 6,000 sq ft every 4 hours - twice as fast as traditional steel or concrete. This minimized labor hours, field coordination, and the time the project carried construction financing.
✅ Stronger Materials = Less Materials:
"After doing independent structural testing in accordance with ASTM 119 standards that proved MPP to be more than two times stronger than CLT, we were able to make several improvements to an innovative, point-supported column connection to the floor panel; the beams were eliminated, saving 21” floor-to-floor; the floor thickness was reduced by 1” and the total number of columns were reduced by 630.” - Andrew Ball, oWOW
And that translated into direct savings on the project.
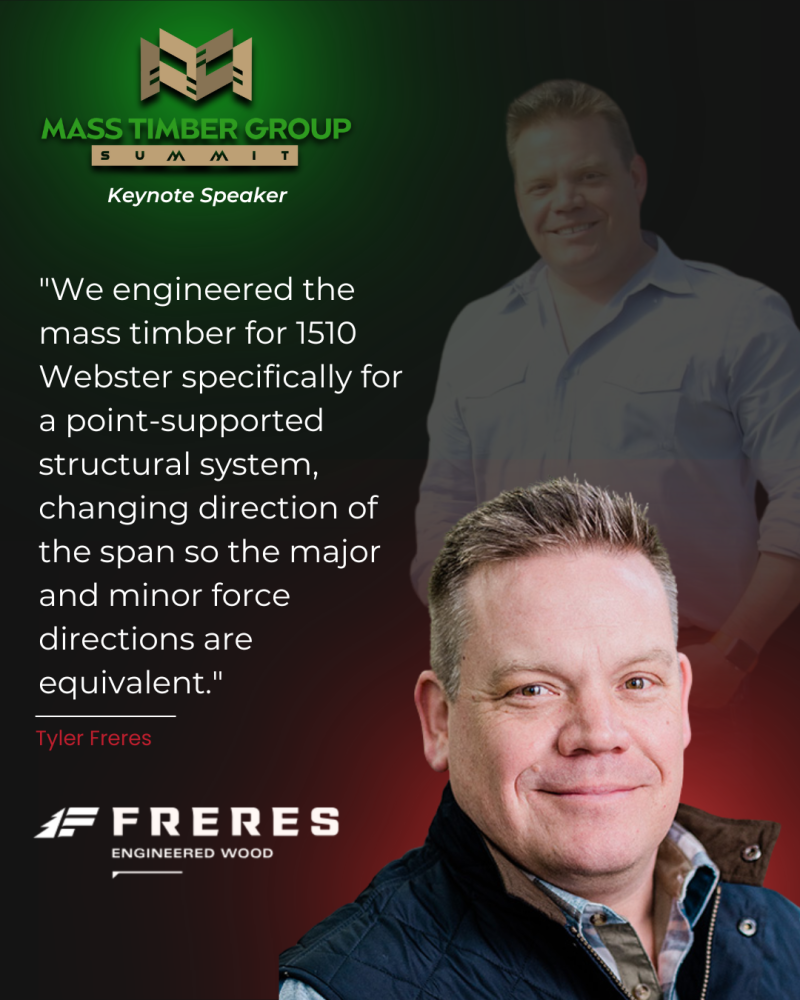
Speed = Financial Competitiveness at Platte Fifteen
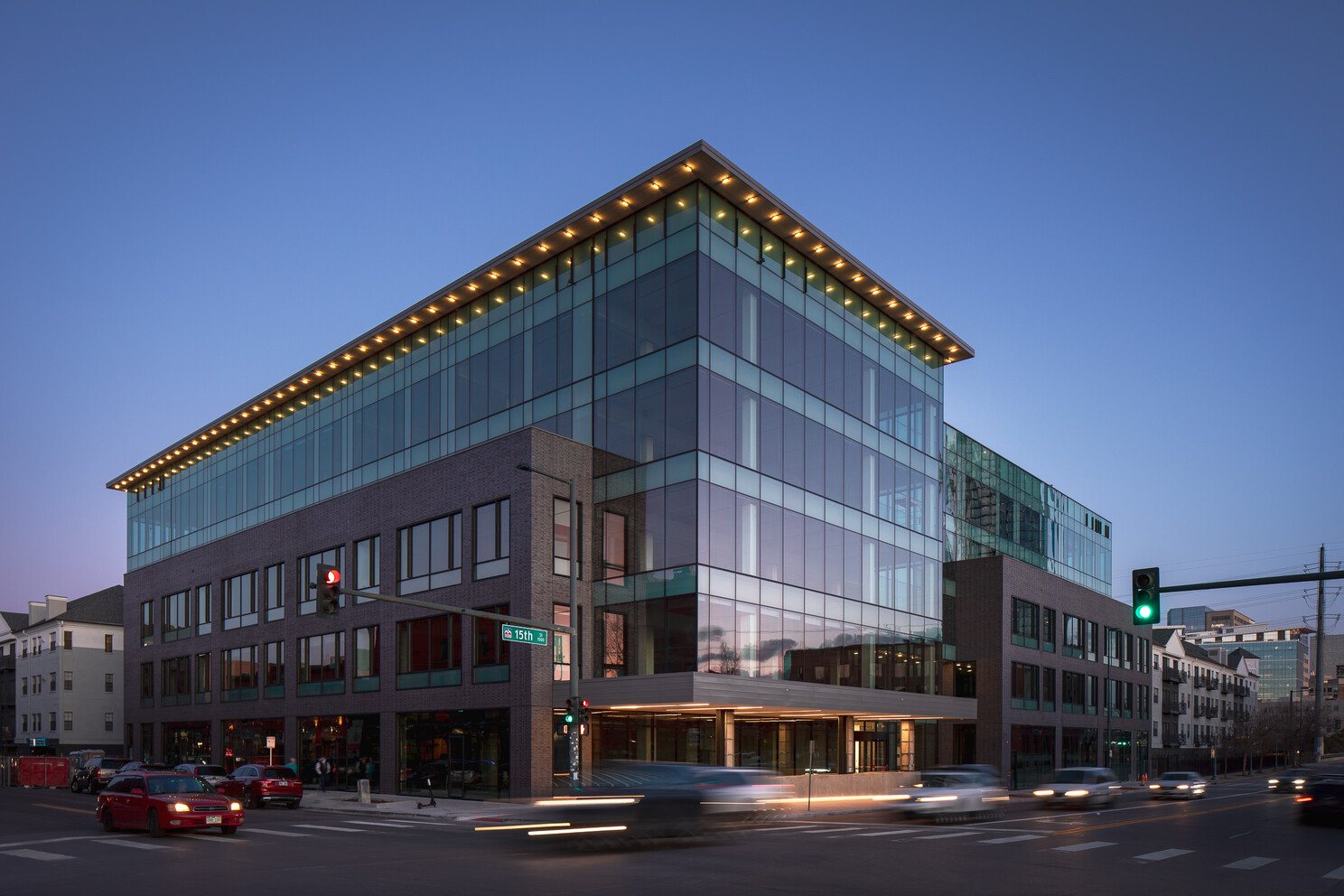
This advantage isn’t unique to Webster.
At Platte Fifteen in Denver, the project team delivered a 25% faster build compared to steel and shaved 3.5 months off a comparable concrete schedule — directly reducing financing costs and accelerating lease-up.
Mass timber’s prefabrication doesn’t just speed up structure — it reduces risk across the board:
✅ Faster dry-in = less weather exposure
✅ Prefab panels = fewer trades and faster sequencing
✅ Fewer deliveries = smoother logistics on urban sites
Less Finish Work = Competitive Interiors
There’s another hidden benefit: exposed timber finishes. Mass timber’s aesthetic means less need for drop ceilings, drywall, or heavy interior finishes — all while tenants actively pay premiums for the look and feel of exposed wood.
What Return to Form Proves
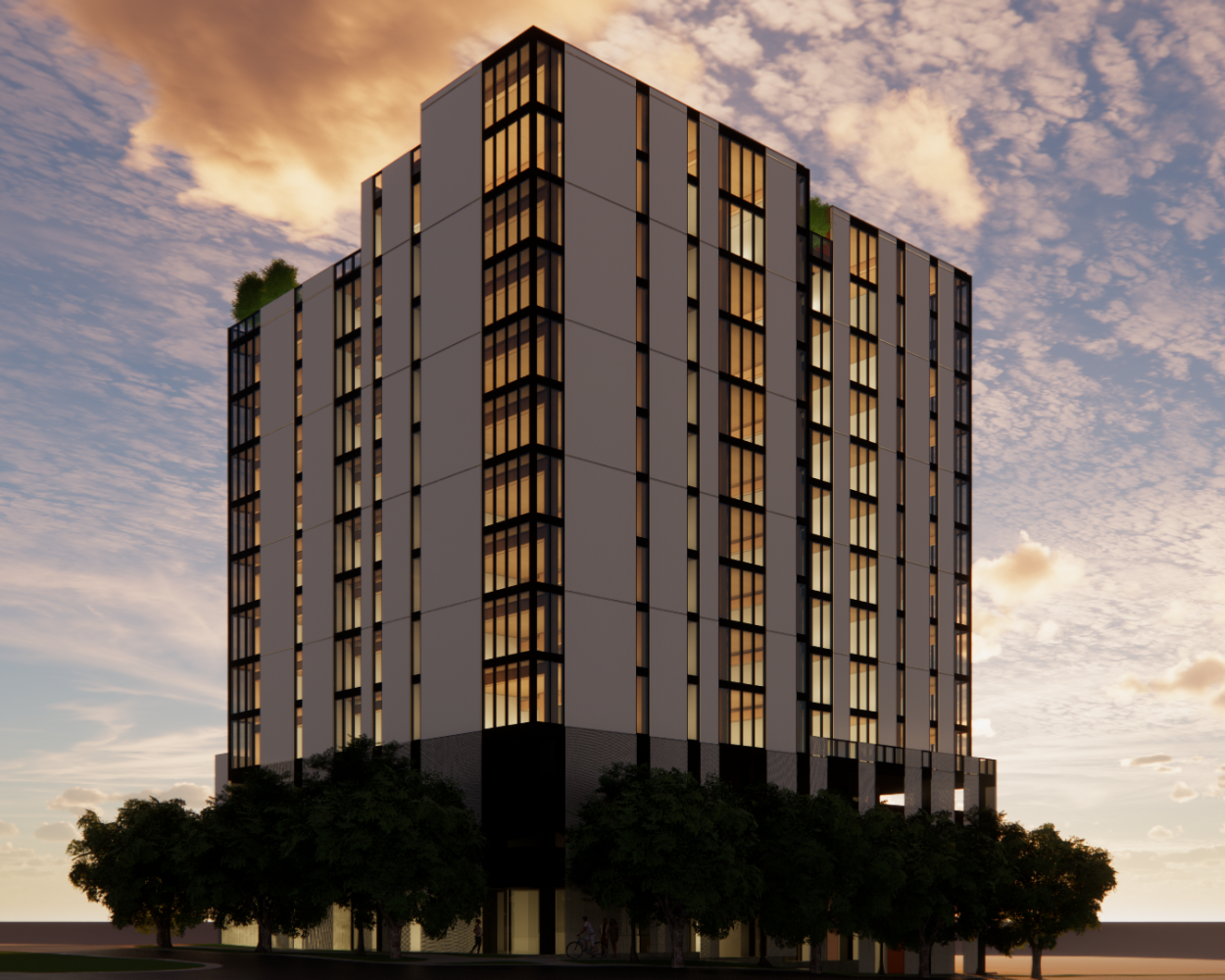
Projects like Return to Form — a planned 12-story residential tower in Denver — are modeling this complete financial picture before ground even breaks.
Pro forma comparisons for the project show total development costs for mass timber within 0.2% of concrete once time, labor, foundation, and interior savings are factored in. That’s not a discount — it’s cost neutrality with major upside in speed, aesthetics, and carbon performance.
The Real Cost Picture — It’s All About Total Value
If your team is only comparing structural material costs in isolation, you’re not seeing the full story.
The actual cost equation for mass timber includes:
✅ Faster schedules = lower financing carry costs
✅ Lighter structure = smaller foundations and reduced excavation
✅ Fewer trades = lower coordination and labor costs
✅ Exposed finishes = reduced interior fit-out
✅ Tenant demand = faster lease-up
✅ Market differentiation = premium rental rates & easier marketability
The Takeaway
Mass timber doesn’t need to “beat” steel or concrete on material cost alone — because that’s not how smart developers evaluate projects. When you account for total project economics — speed, risk, finishes, and tenant demand — mass timber can stand toe-to-toe with any structural system.
That’s exactly the financial reality we’ll unpack at the 2025 Mass Timber Group Summit, where the teams behind these projects just like these will share their real-world numbers and lessons learned.
👉 Secure Your Spot at the Summit
Myth 2 : Mass Timber is Only for Large Buildings - is being debunked next week.
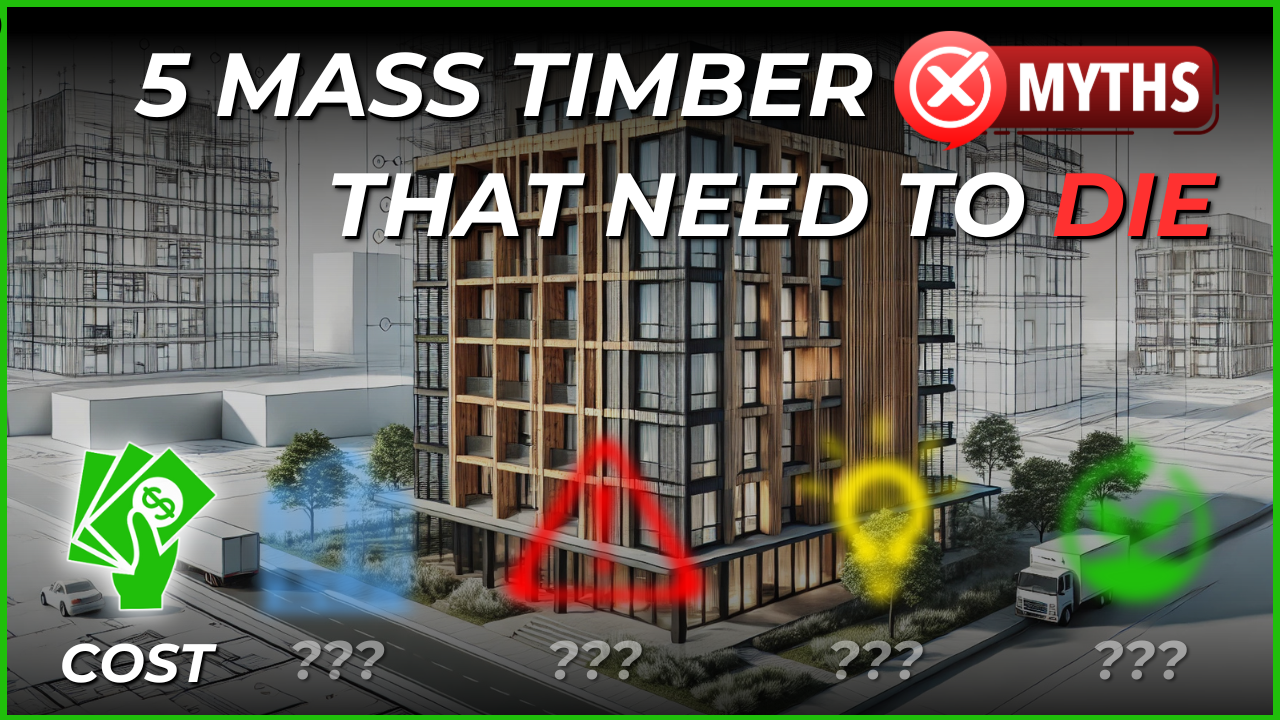
A Norwegian Welcome: The Vesterheim Commons' Soaring Mass Timber Canopy
In the heart of Decorah, Iowa, a town steeped in Norwegian-American heritage, a new architectural gem has emerged, seamlessly blending tradition with contemporary design. The Vesterheim Commons, an 8,000-square-foot addition to the National Norwegian-American Museum and Folk Art School, stands as a testament to cultural preservation and innovative construction, prominently featuring the sustainable and aesthetically pleasing qualities of mass timber. Designed by the New York office of the acclaimed Norwegian architecture firm Snøhetta, in collaboration with Kansas City-based BNIM as the architect of record, the Commons offers a dynamic new entry point and gathering space for the institution, solidifying Decorah’s position as an unassuming center for Norwegian-American culture.
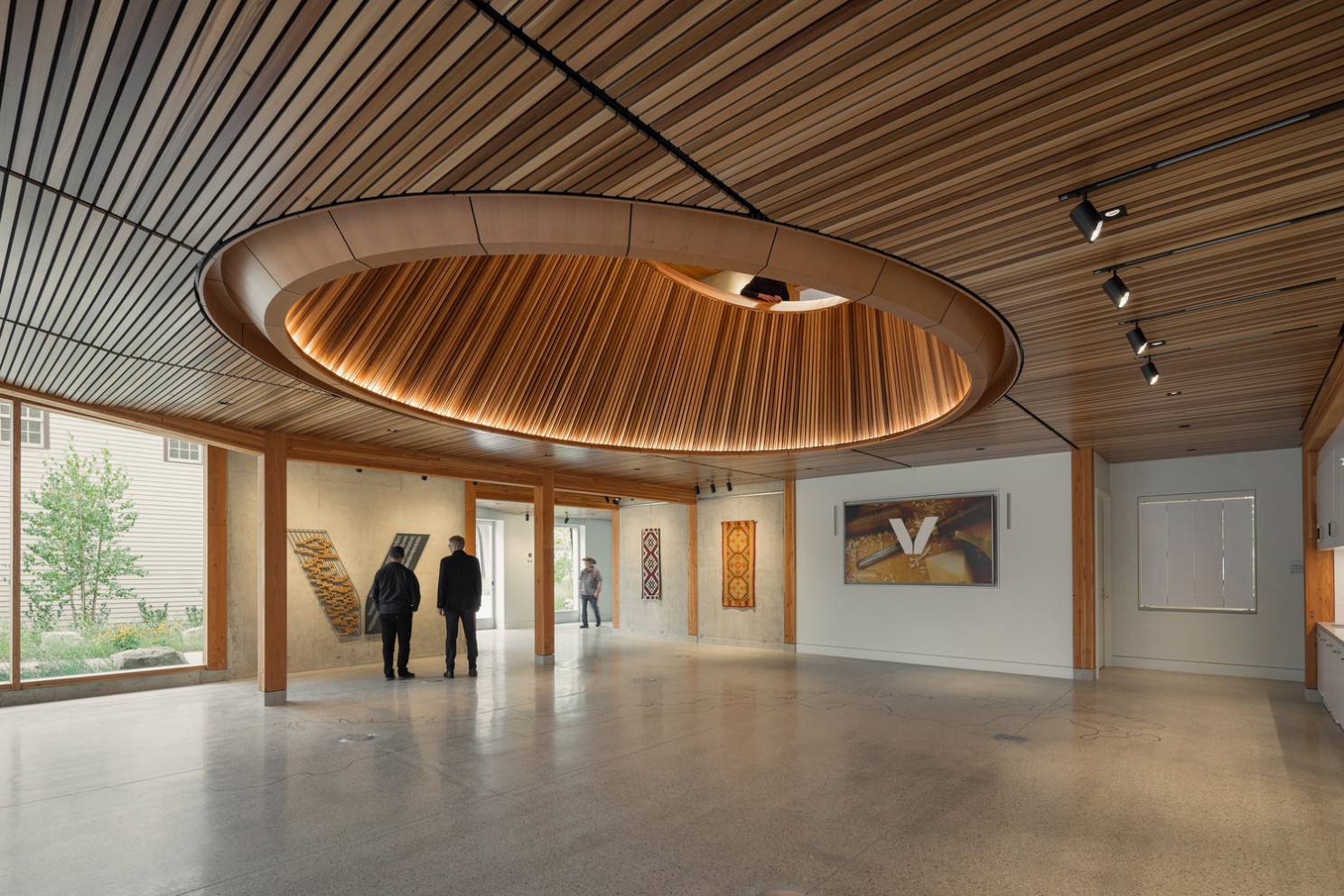
A Historical Backdrop Meets Contemporary Design
For a town whose population swells tenfold each July for Nordic Fest, Vesterheim has long been a year-round anchor, claiming to be the single-largest museum in the country dedicated to a single immigrant group. Snøhetta’s master plan, completed in 2019, aimed to unify the museum’s disparate buildings, and the Vesterheim Commons, was completed in September 2023.
The masonry-clad addition, extending the scale of the existing 19th-century structures along Water Street, conceals a remarkable secret within its walls: a mass timber frame fabricated in Albert Lea, Minnesota. This deliberate choice of material not only speaks to the tradition and craft of Norwegian-American culture but also underscores a commitment to sustainability.

The Beauty and Benefits of Exposed Mass Timber
Visitors are immediately drawn to the south and west sides of the new building by a swooping cantilevered canopy, an architectural flourish designed to invoke traditional Norwegian boats. This inviting entrance not only provides shelter but also boldly reveals its glued-laminated timber. According to Snøhetta project leader Chad Carpenter, “Expressing the laminated beams, decking, and columns started a visual framework of seeing the exposed structure as you go through,”. This exposed interior structure showcases a blend of Douglas fir and western red cedar. For the canopy and the first-floor storefront columns, which bear the brunt of the elements, Alaskan yellow cedar was chosen for its durability and clean grain, Carpenter noted.
The intentional use of mass timber extended beyond structural elements. Wood mullions proved to be a more economical and sustainable choice than a conventional aluminum curtainwall system at the entrance. “Because we had this conversation going with a glulam fabricator, we were able to engineer mullions out of glulam sticks that were like chopsticks to these guys,” Carpenter explained, from ThinkWood. He further emphasized that wood emerged as the superior material, boasting a lower carbon footprint, a warmer aesthetic, and a lower cost compared to metal. “That was a fortunate bonus,” Carpenter from ThinkWood.
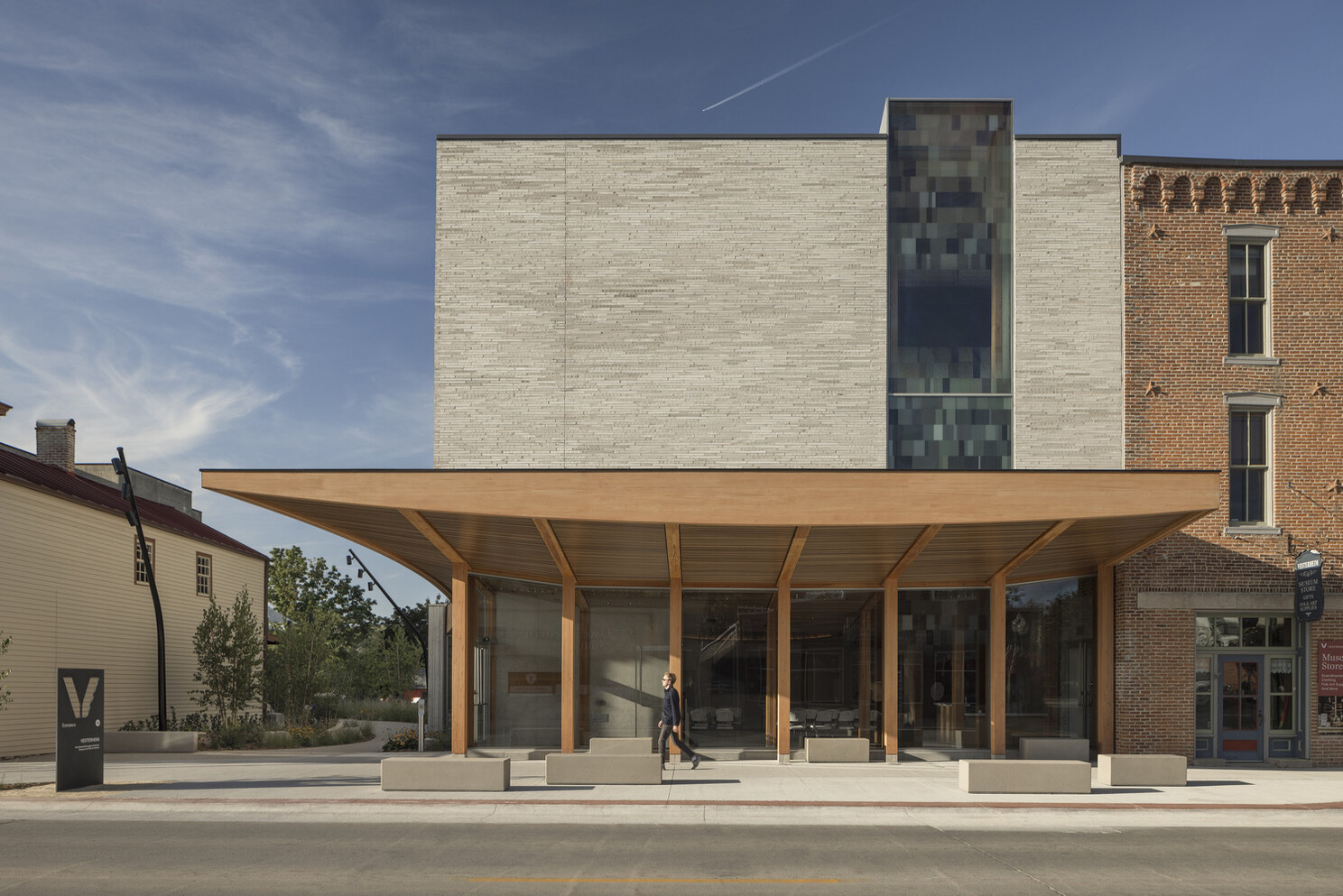
Sustainability Woven Throughout
The 8,000 square-foot, three-story Vesterheim Commons houses a variety of spaces designed to enhance the museum experience. The ground floor features a gift shop and event space that opens to Water Street and a west-side plaza. This lobby, described by Snøhetta’s project lead Matt McMahon, offers a “cool respite from the hot sun outside” on opening day. He also highlighted the design’s solar strategies, noting how the wood-slat ceiling rises to bring in more daylight, while the canopy provides shade in the summer and allows lower winter sun to penetrate deeply into the lobby.
The architects collaborated with Arup to line the oculus’s interior with cedar planks of varying sizes to effectively diffuse sound. This oculus allows natural light to flood the lobby, creating a welcoming and airy atmosphere. The second floor is primarily configured as open gallery space, while the third floor accommodates a classroom, studio, and offices, including a collection study space and digital lab to broaden the reach of Vesterheim’s collections.
Architectural Gestures Rooted in Culture
The design of the Vesterheim Commons is deeply rooted in Norwegian culture. The welcoming canopy, inspired by the designs of renowned Norwegian boats like the Colin Archer boat and the Restauration craft, creates a protected and highly visible entry. The mass timber frames with concrete footings are reminiscent of the stone foundations of the Norwegian “stabbur,” traditional storehouses. Even the textured concrete used in the walls draws inspiration from the work of Erling Viksja, the architect of Norway’s national government building. Inside, the oculus’s form is said to resemble Saami tents, known as “Lavvu”.
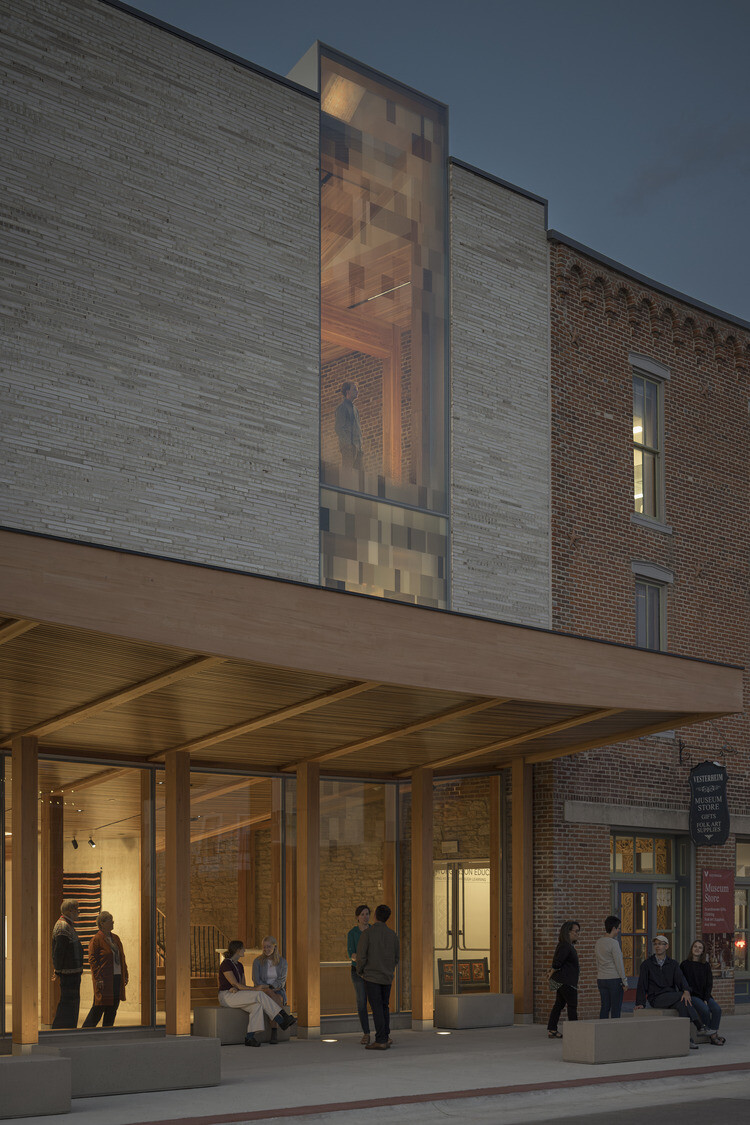
Unifying the Campus and Enhancing the Visitor Experience
The project not only provides functional spaces but also strengthens the connection between the museum collection and the Folk Art School. This integration aims to enrich the visitor experience, both for those physically present in Decorah and those participating digitally through the new video and photography production studio. The Commons also creates a central outdoor gathering space, unifying the campus and extending Vesterheim’s Heritage Park with Water Street. The Heritage Park’s urban woodland, inspired by the similarities between the Driftless region of Northeastern Iowa and the wooded landscapes of Norway, further reinforces this connection to the land.
Crafted with Local Materials and Regional Expertise
Construction of the Vesterheim Commons began in March 2022 and concluded with its public opening in September 2023. While specific figures for the amount of timber used and the project's budget are not explicitly stated in the provided sources, the consistent emphasis on the extensive use of glulam beams, columns, and GLT panels, along with light-frame wood construction, clearly indicates a significant commitment to mass timber in this project.
According to Chad Carpenter, “There’s an optimism in the client and in the place, and that is what we wanted to really see in the building,” - ThinkWood. The monumental treatment of timber in the canopy and the simple palette effectively draw visitors into the building, creating an iconic image that reflects the town, its traditions, and its unique community.
Vesterheim Commons stands as visionary design, with respect for cultural heritage, and a commitment to sustainable building practices can converge to create a truly exceptional place. The innovative use of mass timber not only significantly reduces the building's environmental footprint but also imbues it with a tangible warmth and character that deeply resonates with the cultural narratives it safeguards. This project is far more than an addition; it represents reinvigoration of Vesterheim’s enduring mission, seamlessly connecting the past with the future and fostering meaningful connections between the local community and a global audience.
Project Team and Contributors:
- Design Architect: Snøhetta
- Architect of Record: BNIM
- Structural Engineer: Fast + Epp, MBJ Engineers
- Acoustic Specialist: Arup
- Contractor: McGough Construction
- Mass Timber Fabricator: Bell Structural Solutions
- Brick Fabricator: Glen-Gery Brick
- Mason: Berger Masonry
- Concrete Fabricator: Wicks Construction
- Entry Sign Woodworker: Jock Holmen
- Vesterheim Curtain Wall Contractor: W.L. Hall
- Glass & Custom Frit: Agnora
- Cost Consultant: Directional Logic
- Landscape Contractor: 2nd Nature
- Heritage Park Phase I Landscape Architect: Damon Farber
- MEP Engineering: Morrissey Engineering
- Lighting Engineering: Morrissey Engineering
- Civil Engineering: Erdman Engineering
- Sustainability Consultant: Atelier 10
- Photographer Credits: Michael Grimm
- Client: Vesterheim, National Norwegian-American Museum, and Folk Art School
Frequently Asked Questions (FAQs):
- What type of mass timber was primarily used in the construction of Vesterheim Commons? The primary mass timber components were glue-laminated timber (glulam) beams and columns, as well as glue-laminated timber (GLT) panels.
- What were the key strategies employed to minimize the environmental impact of the building? Significant efforts were made to prioritize wood over more carbon-intensive materials like steel and aluminum, not only in the exposed structure but also in the interior partitions, which utilized conventional light-frame wood construction.
- What is the significance of the oculus in the interior design of Vesterheim Commons? The interior wood oculus serves as a striking architectural feature that visually connects the ground and second floors, while also allowing natural light to flood the lobby area. Its design draws inspiration from elements of Norwegian cultural heritage, including the shape of ship prows and the traditional Saami "Lavvu" tents.
- When was the Vesterheim Commons project officially completed and opened to the public? The Vesterheim Commons was completed and opened its doors to the public in September 2023.
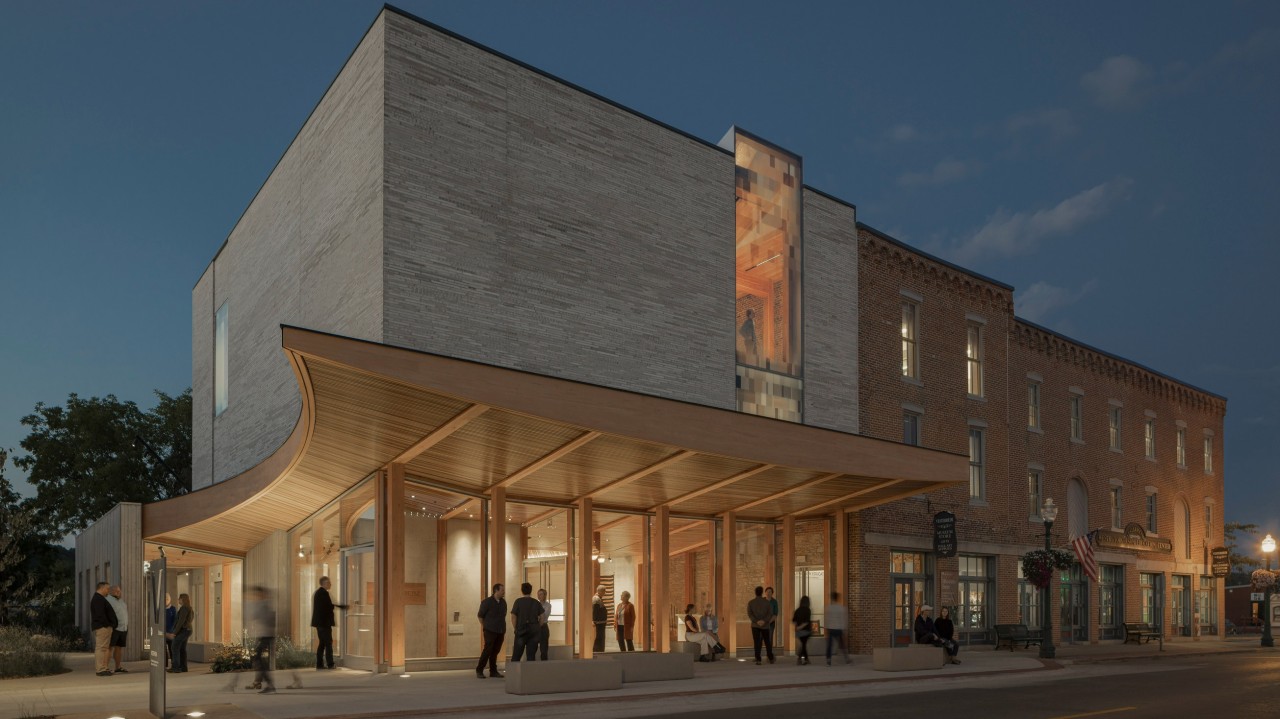