Level up your mass timber IQ & stay up-to-date on industry trends
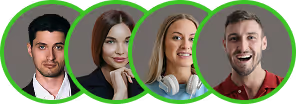
Rising from the heart of Atlanta's Old Fourth Ward neighborhood, 619 Ponce stands as a testament to the burgeoning potential of mass timber construction in the United States.
This four-story marvel, nestled beside the historic Ponce City Market, isn't just a beautiful addition to the Atlanta skyline; it's a pioneering project redefining sustainable construction in Georgia.
Developed by Jamestown, a design-focused real estate investment and management firm, 619 Ponce boasts 87,000 square feet of office space and 27,000 square feet of retail space – a vibrant hub for businesses and shoppers alike. What truly sets this project apart, however, is its innovative use of locally sourced Southern Yellow Pine (SYP) for its mass timber structure.
“StructureCraft played a key role in delivering 619 Ponce, Georgia's first locally grown mass timber project. Utilizing Southern Yellow Pine (SYP) for glulam posts, beams, purlins, and CLT floor and roof panels, the 30'x30' structural grid features a purlin-on-girder system, allowing, efficient MEP integration and reduced timber volume with 4 1/8" CLT panels.” - Benjamin Epp, StructureCraft Business Development Coordinator.
While mass timber construction is gaining traction globally, sourcing timber typically involves importing from the United States Pacific Northwest, or countries like Canada, Austria, and Germany. Jamestown flipped the script, choosing to utilize Georgia-grown timber and a regional supply chain – a first for mass timber construction in the state. This decision drastically reduces transportation emissions and the project's overall environmental impact, maximizing the sustainability benefits inherent to mass timber.
"By sourcing our timber locally, we’ve been able to reduce our carbon footprint while supporting local businesses and our state’s thriving forestry industry," says Michael Phillips, president of Jamestown.
The journey begins with SYP harvested from Georgia forests, including timberland owned and sustainably managed by Jamestown near Columbus, Georgia. Jamestown's commitment to responsible forestry is evident in their adherence to the 2022 Sustainable Forestry Initiative (SFI) Forest Management Standard, which provides third-party verification of their sustainable forestry practices across their 100,000 acres of timberlands.
The harvested timber is then processed into lumber at Georgia Pacific’s sawmill in Albany, Georgia, and subsequently transformed into Cross-Laminated Timber (CLT) panels and glulam columns, beams, and purlins at SmartLam North America’s mass timber plant in Dothan, Alabama. Some glulam members even undergo further fabrication at a specialty timber facility in Rockwood, Tennessee before finally making their way to the Ponce City Market site for installation.
The choice to embrace mass timber extends beyond sustainability. Architects at Handel Architects selected timber for its aesthetic warmth and its ability to maximize daylight within the office spaces. The exposed wood creates a welcoming and naturally bright ambiance for tenants.
“Pre-assembled column, beam, and purlin connections streamlined installation, allowing the structure to be erected in just 12 weeks with a small crew led by StructureCraft despite site constraints, crane sharing, and limited daily erection windows.” - Benjamin Epp, StructureCraft Business Development Coordinator.
The project prioritizes human health by minimizing chemicals of concern in building materials, especially for high-touch interior elements. The material palette, featuring mass timber accented by a natural zinc facade, prioritizes the reduction of embodied carbon and supports the local economy through sourcing materials from within 100 miles whenever possible.
StructureCraft collaborated with Jamestown and Handel Architects to assess the carbon impact of 619 Ponce's timber elements compared to a concrete baseline. The results are striking: the timber gravity system used in the final design achieved a nearly 75 percent reduction in carbon emissions compared to an equivalent concrete gravity system.
Even more impressive is the fact that this calculation doesn't even factor in the carbon captured by the trees during their growth.
“A life-cycle assessment revealed a 75% reduction in carbon emissions compared to a concrete structure, with a net-negative carbon footprint of 1,266 tons, equivalent to removing 300 cars from the road annually.” - Benjamin Epp, StructureCraft Business Development Coordinator
Its location near the Atlanta BeltLine positions it within a rapidly developing area attracting tech companies and new residential high-rises. Sage, a global accounting firm and technology company, has already selected 619 Ponce as the location for its North American headquarters, citing the building's alignment with its ESG values.
"We chose to relocate our North America Headquarters to 619 Ponce because it is an ideal location for a tech center in the heart of this thriving Atlanta community, while also aligning with our ESG values by selecting a mass timber building made from responsibly and locally sourced materials," shares Mark Hickman, managing director of North America for Sage.
Alexandra Kirk, Vice President of Real Estate Development at Jamestown, emphasizes the building's focus on community integration through its ground-floor retail space – a feature not typically found in mass timber buildings. This design choice allows the public to directly engage with the space and experience the beauty of mass timber firsthand.
"It’s amazing to see everyone live through what we believed would happen—that people would love it, that people would want to be here," reflects Kirk.
It paves the way for a future where mass timber, particularly when sourced locally, plays a leading role in shaping our built environment.
This is a partial list of all the individuals and organizations contributing to the 619 Ponce Georgia project. In the comments section, please let us know if you contributed in any way.
Lead mass timber projects with confidence — and leave delays, redesigns, and budget blowups behind.
✅ Solve early-stage design, sourcing, insurance, permitting, code & cost hurdles before they derail your project.
✅ Find technical answers on design, detailing, procurement, embodied carbon ROI, hybrid systems & more.
✅ Build relationships with developers, GCs, architects, and engineers shaping mass timber’s future.
Get your ticket— and get the insights, skills, and network to deliver mass timber projects successfully.