Level up your mass timber IQ & stay up-to-date on industry trends
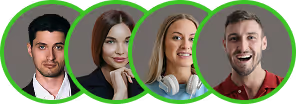
So, here we are—another round of tariffs shaking things up. This time, the U.S. has slapped additional duties on imports from Canada, Mexico, and China, and it’s causing quite a stir in the construction world, especially for those of us working with mass timber. The official line is that these tariffs are part of a broader strategy to address illegal immigration and drug trafficking. But what do they really mean for our industry, and how do we navigate the fallout? Let’s break it down.
According to the White House, the U.S. is imposing a 25% additional tariff on imports from Canada and Mexico and a 10% tariff on imports from China. Energy imports from Canada face a slightly lower 10% tariff. The stated goal? To hold these countries accountable for curbing illegal immigration and the flow of drugs like fentanyl into the U.S.
The fact sheet tees up the situation as a national emergency with public health impacts. The administration is leaning on tariffs as a tool to secure borders and protect American interests, emphasizing that the U.S. already has one of the most open economies and some of the lowest average tariff rates in the world. But in 2023, the U.S. also had the world’s largest trade deficit in goods—over $1 trillion. So, according to them, tariffs are the leverage we need.
If you’ve been in this space for a while, you know the U.S. and Canada have a long, complicated relationship when it comes to wood products. The softwood lumber agreement has been around for decades, dictating when tariffs go up or down. But here’s the catch: it mostly covers lumber, not all wood products.
As Tyler Freres, VP of Freres Wood (Freres Engineered Wood) explained, "Lumber producers were the ones at the table when the softwood lumber agreement was created, but products like veneer, OSB, LVL, and mass timber didn’t get that same focus." That’s why these products have traditionally flown under the radar of U.S.-Canada trade disputes. And guess what? Canadian producers have taken full advantage of that, expanding their production of veneer and panel products—sometimes at the competitive expense of Pacific Northwest producers.
But here’s where it gets tricky. We were already looking at scheduled tariff increases for 2025 - but for lumber only. This duty does not apply to products like LVL, plywood, or other engineered wood products (like mass timber). The duty on softwood lumber was at 14.4% and set to climb to 30% - 40%, later this year. Now, with this new 25% tariff stacked on top, things could get interesting if the two countries can’t strike a new deal. And if they do - its likely engineered wood products revert back to the status quo and remain outside of existing trade agreements.
The U.S. and Canadian wood product sectors have always been connected, but they’re also fierce competitors. Canada supplies about 30% of the lumber used in the U.S. As Hardy Wentzel, CEO of Think Mass Timber, put it, “The U.S. simply doesn’t produce enough lumber to meet its own needs.”
However, U.S. mills and wood product manufacturers may have a different view on the situation. As Tyler Freres says “We have plenty of standing timber, we have an existing lumber infrastructure, would we be importing 30% of our supply if we responsibly managed our forests? We have the capacity to produce more but for the predatory trade actions of foreign countries”
Canada’s reliance on the U.S. market is equally strong. More than half of Canada’s total lumber production heads south, making this tariff situation a serious concern for them. Plus, the Chicago Mercantile Exchange (CME) bases its lumber futures contracts on prices from British Columbia, a major hub for timber production. Since the CME’s contracts are used as a benchmark for pricing across North America, any fluctuation in Canadian lumber prices sends immediate signals to the broader U.S. market.
These price shifts ripple through the entire building industry, affecting everything from construction timelines to material costs. When Canadian prices rise due to tariffs or market disruptions, U.S. domestic producers often adjust their prices upward to remain competitive. This dynamic impacts not only mass timber projects but also general construction costs, making it harder for developers to budget accurately. The result can be delayed projects, reduced profitability for builders, and a slowdown in construction activity—particularly for large-scale or timber-intensive developments.
Canadian companies have also been making moves in the mass timber space, especially in the Pacific Northwest, where they’ve leveraged their previous tariff exemptions on products like CLT, glulam, and LVL. But with the new tariffs potentially applying to these products, that competitive edge could shrink.
Here’s the thing about tariffs—they don’t just make imports more expensive. When the cost of imported goods goes up, domestic producers often raise their prices too. As Hardy Wentzel pointed out, “When the U.S. put tariffs on South Korean washing machines, the price of American-made machines went up too, along with the price of dryers, even though they weren’t tariffed.”
Expect a similar pattern here. The 25% tariff on Canadian lumber is likely to push prices higher across the board, even for domestically produced lumber. And since mass timber depends heavily on lumber and other wood-based inputs, those price hikes could ripple through our entire sector.
Projects already underway? They might be in for some tough budget conversations. And for new projects, developers may think twice about committing if costs climb too high. But, as Freres points out - if there were no escalation clauses in the contracts for existing projects- the manufacturers may be forced to eat the price increases brought on by the tariffs. Finally, Nicholas Sills of Whirlwind Consultants pointed out, "This uncertainty could really slow down mass timber’s market adoption."
Unlike your typical trade dispute, this one is wrapped in national security rhetoric, making it harder to predict how long the tariffs will last. The White House has made it clear that these tariffs will stay in place until there’s real action on the issues they’re targeting. For now, both Canada and Mexico have secured a 30-day pause on the tariffs, giving officials time to negotiate potential agreements.
Canada isn’t sitting idle in the meantime—they’ve matched the U.S. with their own 25% counter-tariffs on American goods, keeping the pressure on. While this pause buys some time, it’s unclear whether the countries can reach a long-term resolution within the window. For now, we’re in a holding pattern, waiting to see if diplomacy can smooth things over or if we’re headed for a longer trade standoff.
We spoke to a few industry leaders to get their take on where things might go from here:
Tyler Freres (Freres Engineered Wood):
Hardy Wentzel (Think Mass Timber):
Nicholas Sills (Whirlwind Consultants):
Mass timber has gained traction as a sustainable alternative in the construction world, but the newly imposed tariffs could make it less competitive compared to traditional materials like concrete and steel. As Hardy Wentzel explains, mass timber projects rely heavily on lumber, which accounts for up to 60% of their variable manufacturing costs. The added cost pressure from tariffs could tip the balance for developers, pushing them to favor cheaper, more established building materials.
Concrete and steel are not without their own price fluctuations. Tariffs applied to oil, an essential component in the heat-based production of these products - will also increase costs. However, the proposed tariff on Canadian oil is stated to be 10%, compared to the 25% that will impact the wood inputs for mass timber. Developers working on tight budgets may choose these materials to mitigate financial risk, particularly in large-scale projects where mass timber’s initial cost premium already poses a challenge. If the price gap widens too much, Wentzel warns, mass timber’s market adoption could slow, undercutting its role as a sustainable building solution.
There’s no sugarcoating it—the current tariff situation poses serious implications for mass timber and the broader construction industry. Canada accounts for half of North America's mass timber manufacturing capacity, and as Wentzel argues “[these tariffs make a major] obstacle to industry growth. A 25% tariff will inflate prices in both countries, diminishing mass timber's competitiveness to steel and concrete, slowing adoption in the U.S.”
But as Tyler Freres argues, the market will eventually adjust. Innovation, local sourcing, and better forest management could bridge the gap.
Wentzel aptly summarized the situation as such; “Whether these tariffs are a temporary disruption or long-term obstacle remains uncertain. Regardless, the industry must adapt and innovate to sustain the momentum mass timber has built over the past decade, ensuring its viability as a future-forward and sustainable building solution.
Author
Lead mass timber projects with confidence — and leave delays, redesigns, and budget blowups behind.
✅ Solve early-stage design, sourcing, insurance, permitting, code & cost hurdles before they derail your project.
✅ Find technical answers on design, detailing, procurement, embodied carbon ROI, hybrid systems & more.
✅ Build relationships with developers, GCs, architects, and engineers shaping mass timber’s future.
Get your ticket— and get the insights, skills, and network to deliver mass timber projects successfully.